An Israeli startup is developing a way to make brand new plastic products from the moth-eaten shirts, torn pants, and other unwanted clothes that we normally throw away.
TextRe uses synthetic fibers such as polyester and nylon from textile waste, and combines them with certain substances, including a reduced amount of plastic and other unnamed materials, in order to create plastic pellets.
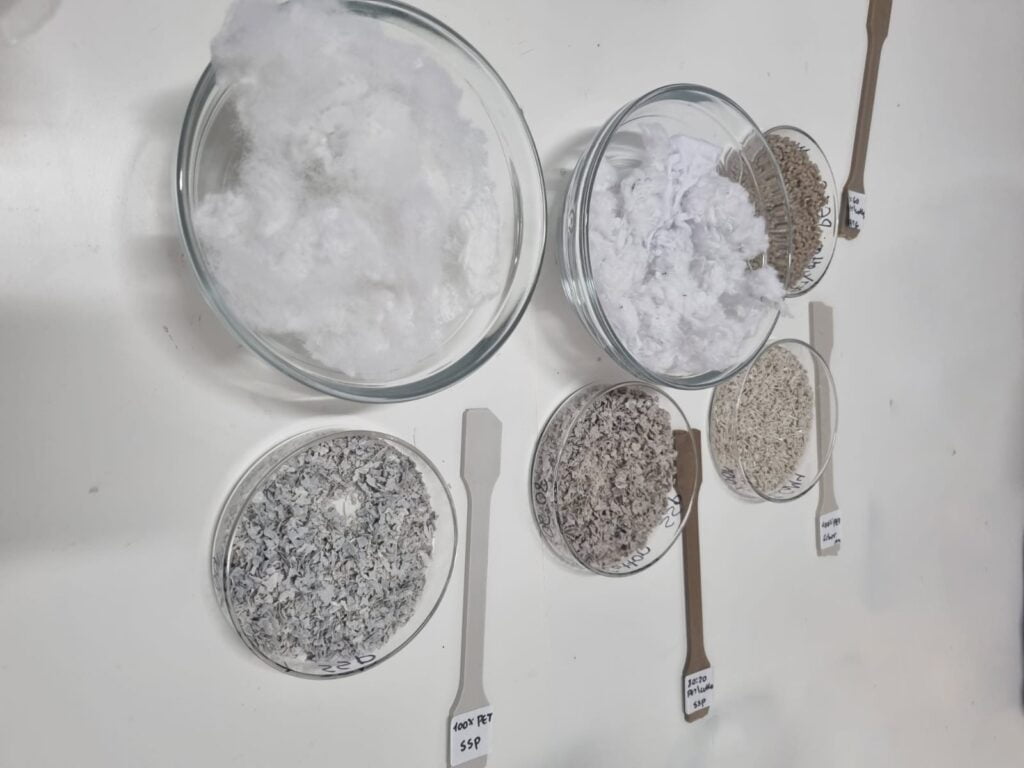
The startup says the process can be seamlessly integrated into the production lines of plastic manufacturing companies, who will mix the pellets with virgin polymers and ultimately produce a more sustainably sourced plastic product.
“Our purpose is to replace the use of virgin materials with recycled ones, and receive the best characteristics [like elasticity and durability] that we can,” Lee Cohen, co-founder and CEO of TextRe, tells NoCamels.
If Looks Could Kill
Of the estimated 100 billion garments produced worldwide every year, close to 92 million tons end up in landfills, according to illuminem, a platform that monitors businesses’ performance on sustainability and ethical issues.
Just one percent of these garments are recycled and around 12 percent are turned into lower quality products such as cleaning cloths, carpet padding and sound insulation.
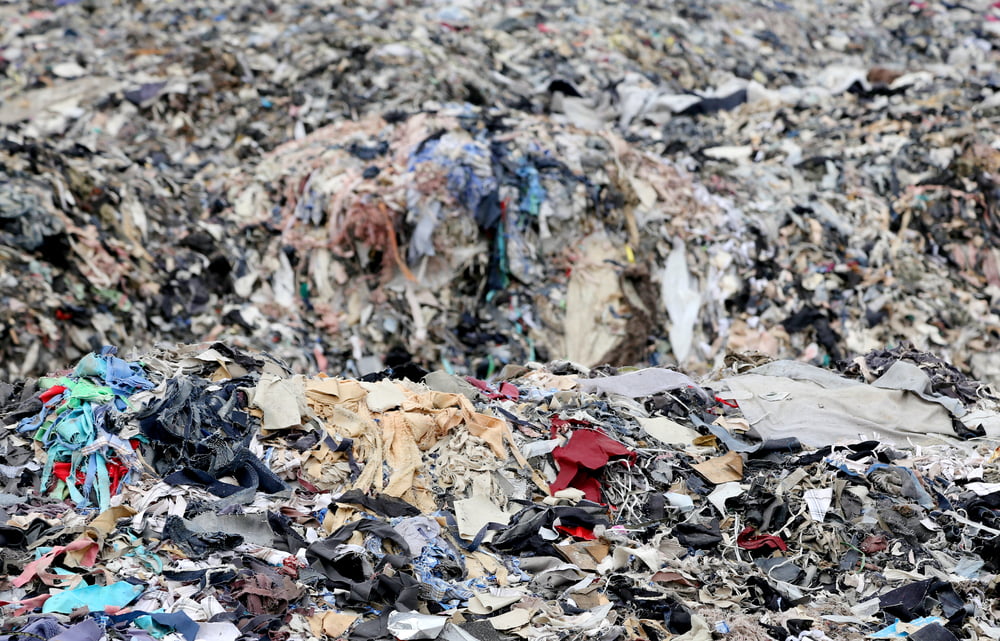
The rest could take hundreds of years to decompose, harming the environment in the process.
To recycle them, synthetic fibers are separated from the piece of clothing, shredded into small pieces of plastic, and then melted down, usually to spin new yarn.
However, few items of clothing are recycled because each one is made of a different combination of synthetic and natural fibers, in addition to having various accessories like studs, zippers and buttons.
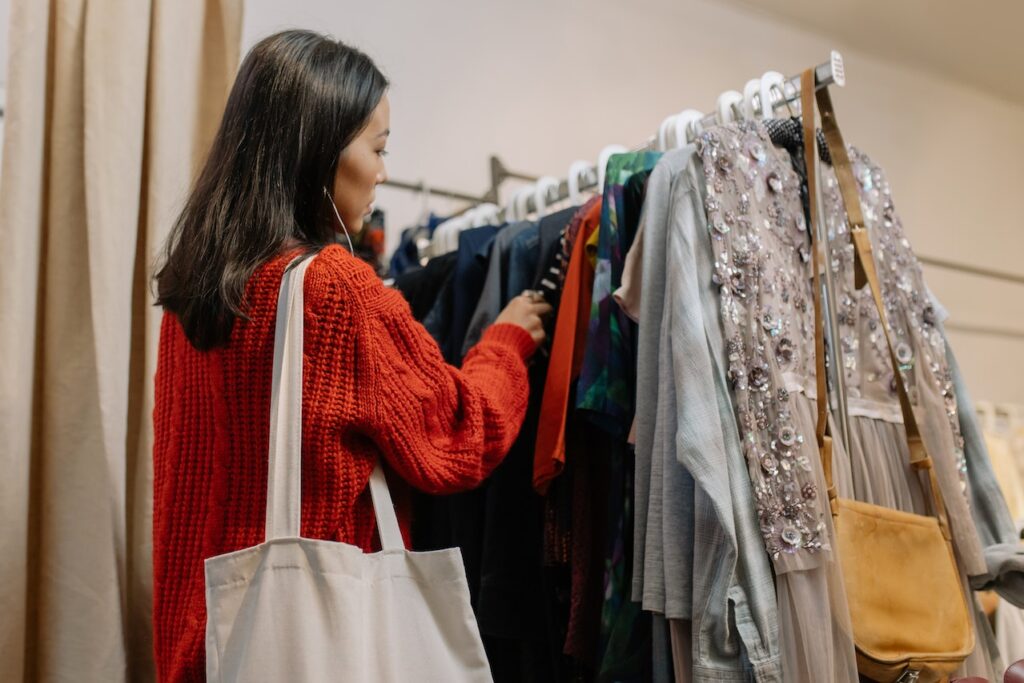
These factors make it a challenge to separate the synthetic fibers from the garment for effective recycling, and the process today is labor-intensive and slow.
But if the materials are not properly separated from one another, they cannot easily be recycled.
“It’s a big challenge, because technology has not developed enough to accurately separate the fibers,” explains Cohen.
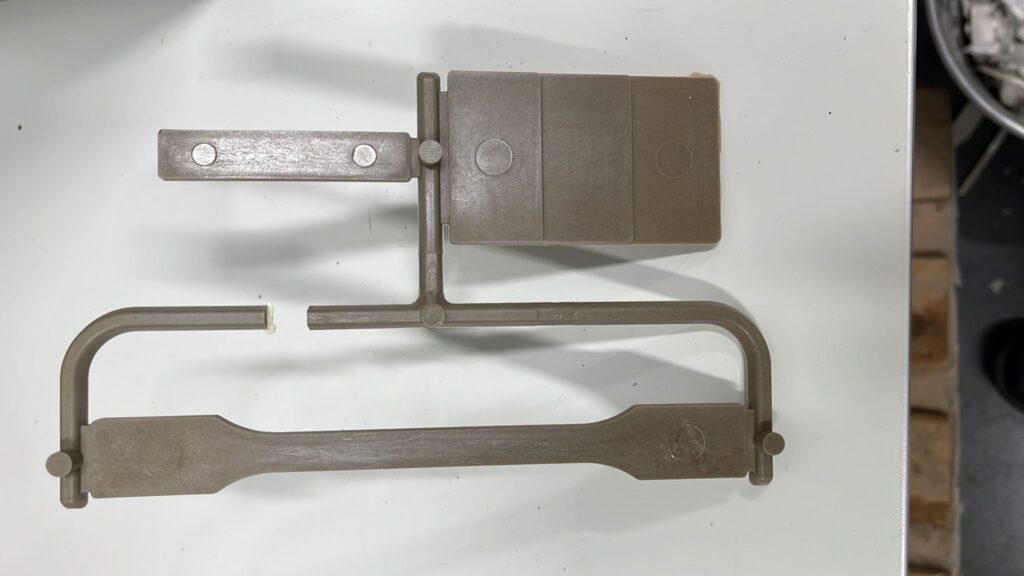
With TextRe, however, the synthetic fibers do not need to be so meticulously separated in order for the startup to effectively turn them into brand new products. This requires much less time and effort than if they were being recycled into a lower-quality product.
The startup’s own tests have shown that their technology can successfully turn the separated synthetic fibers into pellets that are then injected into a mold to create a new plastic product.
In fact, TextRe says it has made prototypes of several plastic pellets that can be used in new products.
“Realizing that most of our clothes are made from plastic – like polyester – made it natural to think of ways to upcycle it for plastic industry applications,” Cohen says.
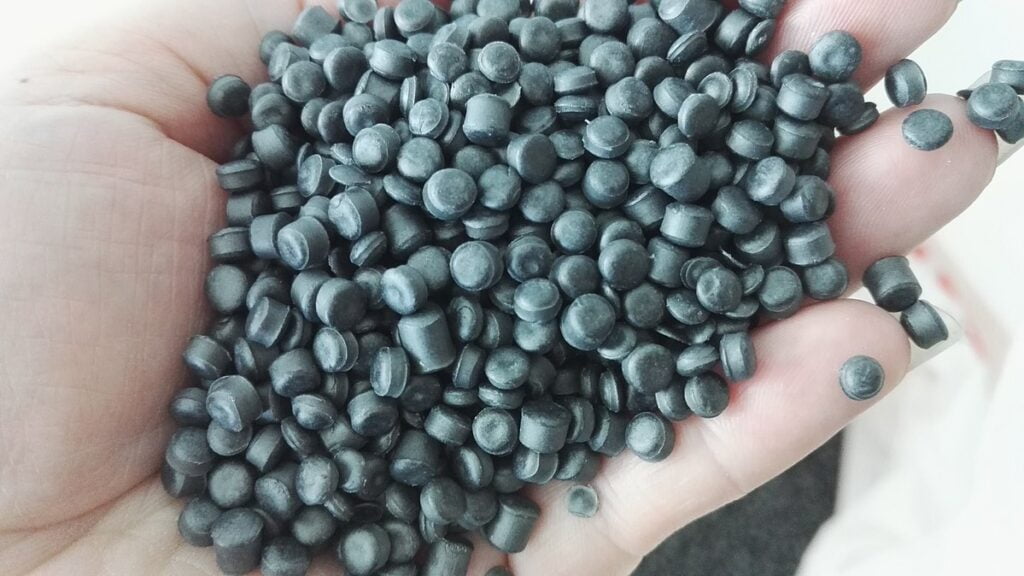
The Tel Aviv-based startup, which was founded in 2021, is now completing a proof of concept to demonstrate its technology’s feasibility.
Sign up for our free weekly newsletter
SubscribeIt is working with a leading Israeli company that produces plastic, which is testing the process on its own production lines.
Cohen declined to disclose more about the process itself, citing company privacy.
Castoff Challenge
End-consumers, companies, and even governments have all been increasingly seeking a solution to the textile waste problem, especially as public awareness has grown in recent years.
The European Commission is drafting at least 16 pieces of legislation that will make fashion companies take more responsibility for the environmental impacts of the clothes they produce.
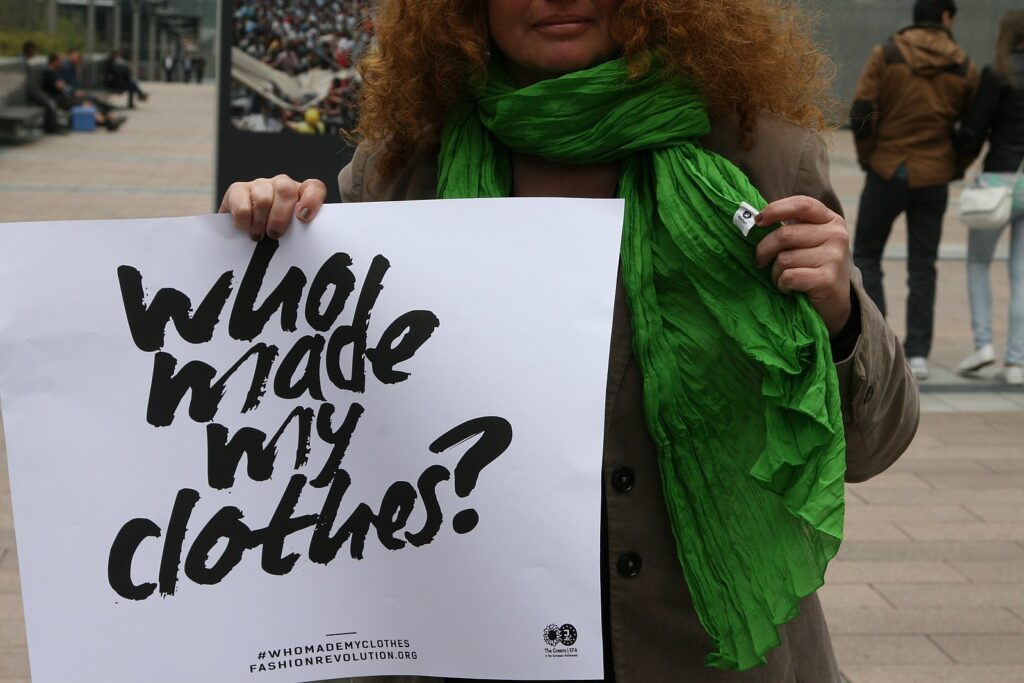
These measures include a requirement for fashion companies to collect a minimal amount of their textile waste rather than discard it all. The governments of European Union member states even agreed that they should ban the destruction of unsold textiles in order to encourage more reuse and recycling.
“This is a great incentive for textile brands to find a solution that they can also earn money from,” says Cohen.
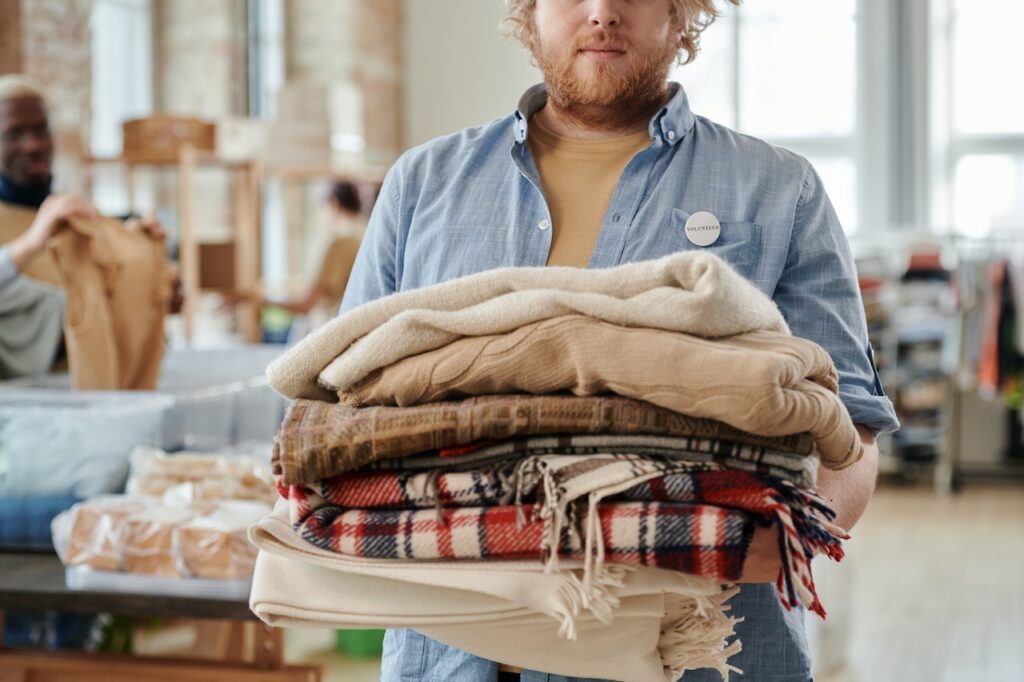
She believes that these regulations also incentivize companies to start replacing virgin materials with recycled ones. She says, however, that there is a dearth of quality recycled substitutes on the market today that hold up when compared to new polymers – which is where TextRe comes in.
“We were able to overcome some of the challenges within the process, given the fact that these fibers have different characteristics than conventional plastic products, which we continue to develop and improve to create valuable recycled plastic products,” says Cohen.
There are a number of existing companies that turn textile waste into new materials.
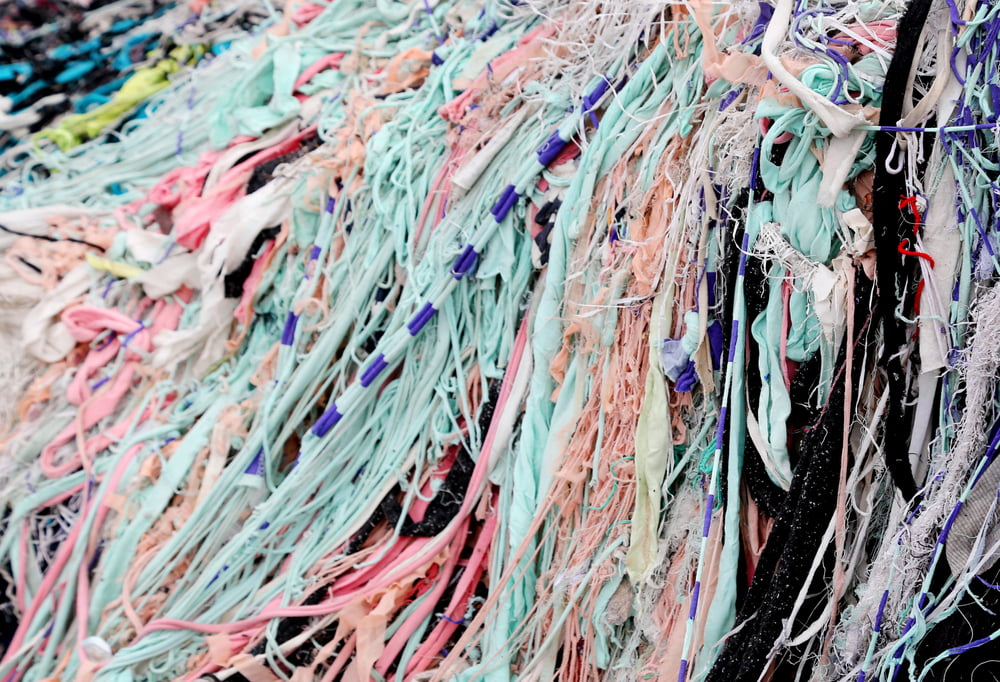
These include Virginia-based Circ, which uses water, pressure, and what it calls “responsible chemistry” to separate synthetic fibers from plant-based materials and turn it into high quality fiber, and German company Kleiderly, which takes clothing waste and recycles it into a sustainable alternative to oil-based plastics.
But Cohen says that solutions such as these involve expensive and unsustainable processes that consume a lot of energy – which is counterproductive to the ethos of sustainability.
In July, TextRe was announced as one of the winners of the 2023 MassChallenge Israel core accelerator program, a four-month intensive program that helps entrepreneurs develop their nascent companies.
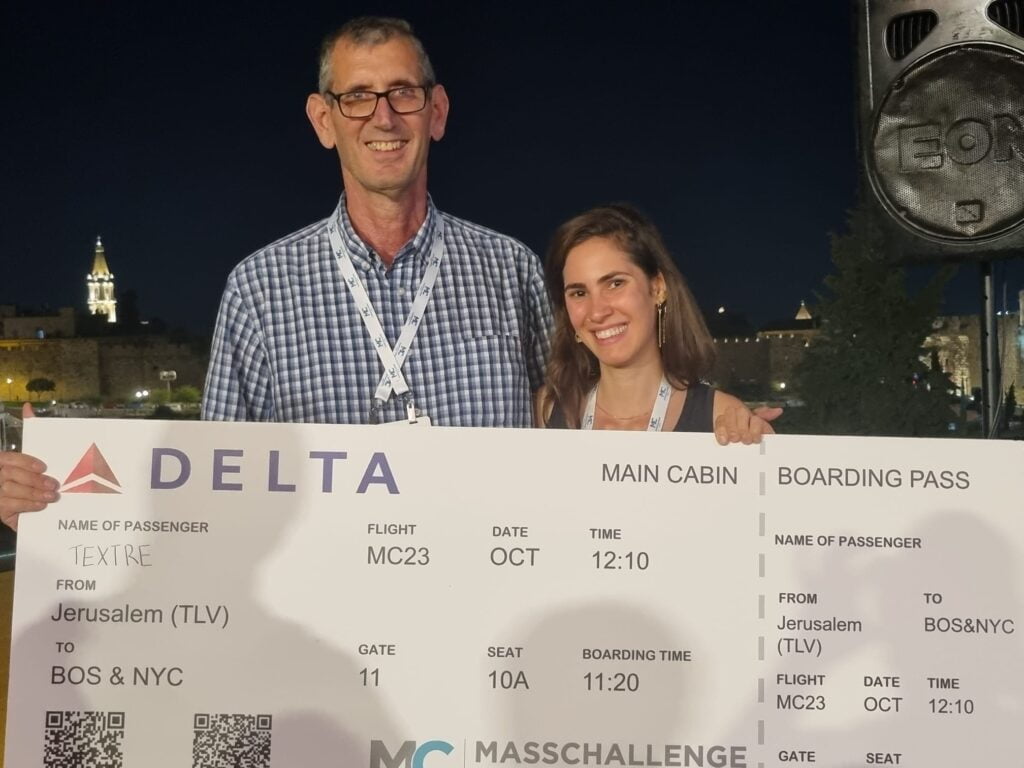
In the coming months, TextRe and the other MassChallenge winners will participate in a roadshow to Boston and New York, where they will meet with investors, customers, partners, and business leaders and officials.
While the startup is primarily bootstrapped, it is presently in the process of fundraising of $2 million, and hopes to bring its product to market within the next 18 months.
“The second largest polluting industry in the world today is the fashion industry,” says Cohen.
“But we believe that this waste can actually be used over and over again as a raw material, instead of continuously sending it to landfills.”
Related posts
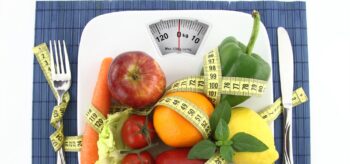
Harnessing Our Own Bodies For Side Effect-Free Weight Loss
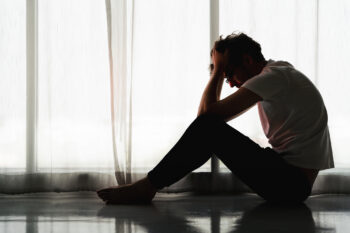
Israeli Device Is New, Drug-Free Solution For Men Coping With ED
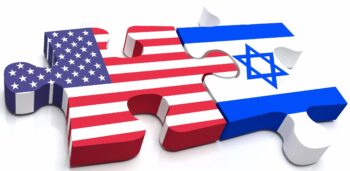
Facebook comments