Startup develops a stay-fresh coating from wood pulp that CAN be recycled
Nanocrystals from wood pulp are replacing the waterproof film that currently makes it impossible to recycle billions of cartons and other items of food packaging.
The cardboard or paper itself is very often recyclable, but it’s impossible to separate it from the thin plastic or aluminum lining that stops liquids leaking out, or air getting into sealed packets of dry goods.
That means millions of tons of waste are being dumped instead of being recycled.
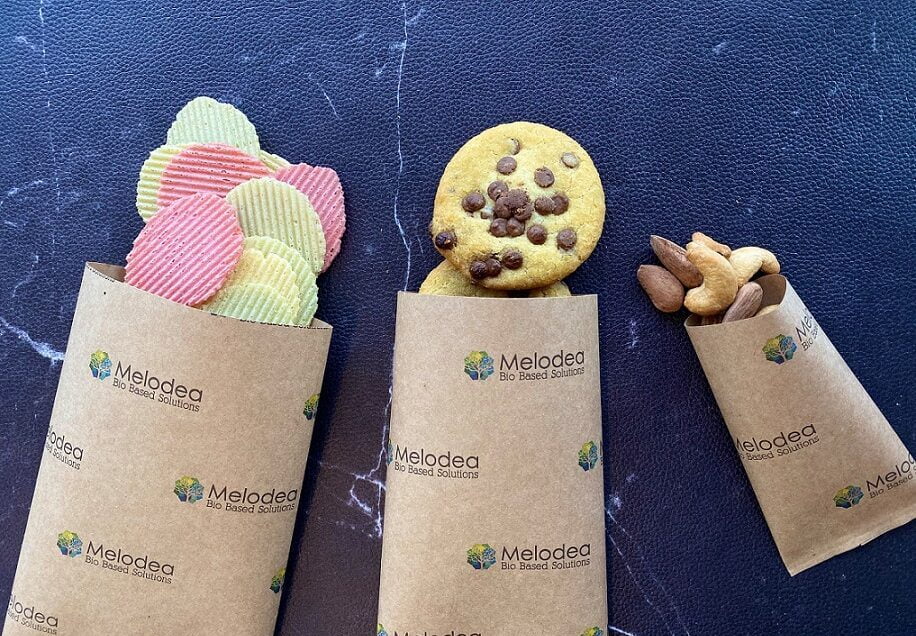
Melodea, a startup based in Rehovot, central Israel, has addressed that problem by developing a unique way of using cellulose nanocrystals (CNCs) – the natural building blocks of all plants – to create a new generation of “barrier coatings” for food packaging.
They do everything that traditional so-called “eco-barrier” coatings do, protecting the contents from oxygen, air and water vapor, but they are fully recyclable.
“You know, if you open a bag of chips, it has this aluminum-facing inside,” says Shaul Lapidot, Co-founder and CEO of Melodea.
“So it’s plastic covered with a very thin layer of aluminum. And that gives you the long-term protection from all of these substances: from moisture, from oil, and from oxygen.
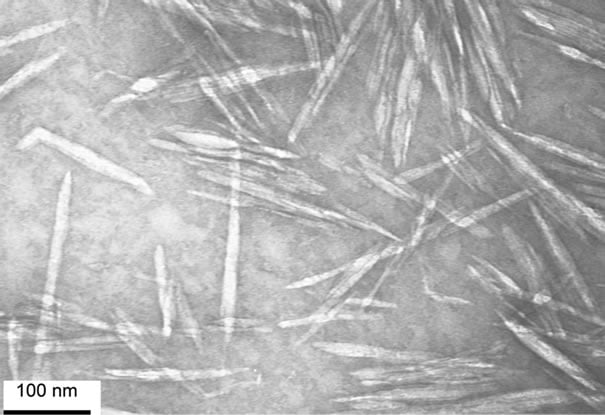
“We apply the same properties by coating plastic or paper with our solution, which is based on materials that we extract from natural fibers, from plant fibers.
“It’s a fraction of the plant fiber that we chemically extract and disperse in water, which is turned into a transparent gel because of the very, very small size of the particles. And we formulate them into products.”
The company extracts CNCs from forestry wood pulp, the raw material used to make paper, on an industrial scale.
It originally used waste products from the paper and forestry industries, but found it was more sustainable and economical to produce it directly from wood pulp.
Wood waste contains a lot of contaminants, and treating it in order to extract CNCs has a heavy environmental and economic cost.
Unlike plastic, which has a significant carbon footprint and a serious impact on our environment, cellulose is both widely available – it is found in all plants – and is biodegradable.
“It comes in the form of sheets, like very thick pieces of paper. We chop it, put it in a reactor, and use acid to selectively extract the cellulose nanocrystals (CNCs),” says Lapidot.
“And then we separate the CNCs from the acid, wash them and we end up with this dispersion.”
Sign up for our free weekly newsletter
SubscribeIt can then be applied to paper, plastic and other packaging. It’s just as effective, and has the same shelf life as non-recyclable coatings.
Other companies have created eco-barrier packaging as well, but Lapidot says that they do not maintain their performance in areas with high humidity. He says that Melodea’s products have the best performance when compared with the competition.
“We have our own environmental chamber where we actually take products and put them there with our coatings for a long period of time, and compare them to the existing eco-coatings in the market. And we have seen that we are better.”
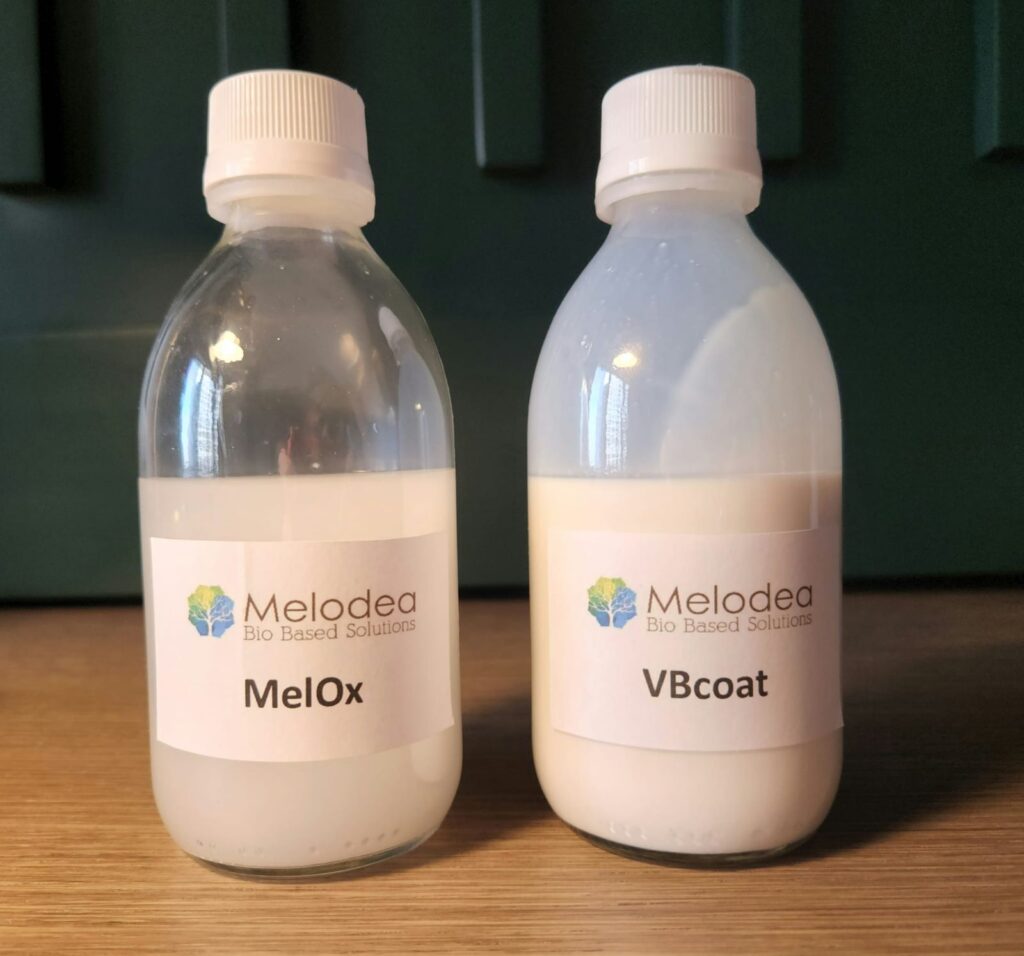
Melodea’s manufacturing plants in Israel can produce hundreds of tons of materials a year. It has recently expanded to a manufacturing plant in the US, where it will boost its production capacity to thousands of tons a year.
It already demonstrated the feasibility of its products in the US, and expects its first commercial products to be used for a variety of packaging in early 2023.
Melodea’s solution is currently being used for the manufacture of paper-based pouches, lids, molded pulp trays, and more.
That said, the barrier coatings have their limitations. They mainly focus on dry products, including coffee beans, chocolate, and hard cheeses, as well as non-food products like washing powders. In the long-term, Melodea aims to expand to liquid packaging too.
Packaging accounts for more than 40 per cent of all plastic produced. Hybrid packaging, which uses primarily paper-based products with a thin plastic layer, serves as a good ecological alternative to it.
But recycling it, which involves the separation of paper fibers from the plastic or aluminum coating, is more difficult and costly than plain-paper recycling.
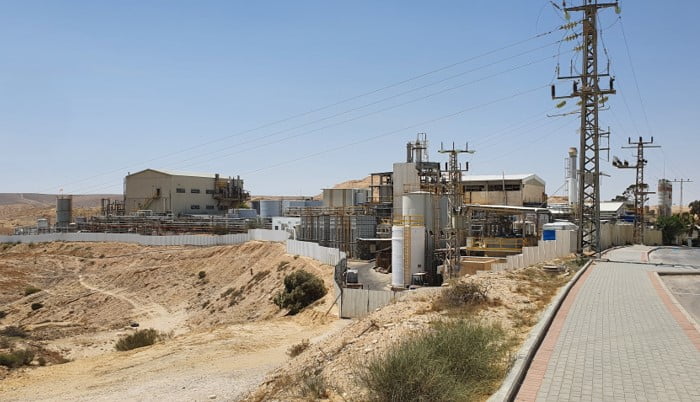
For example, in 2019, less than one per cent of paper cups, trays and dishes made of paper-based hybrid materials were recycled in the EU.
Because these recycling methods are more sophisticated, they need to be collected separately at points of disposal – they cannot be recycled together with regular paper items. And consumers often do not pay close attention to proper recycling guidelines.
“During the recycling process, they wash the plastics before they process them,” Lapidot tells NoCamels. “Our coating is water-washable – it just goes away, and then you can simply recycle the plastic.”
Melodea has several customers, a majority of which are in the US. It also has a pipeline of other products based on CNCs, and is working on applications for electronics, like touchscreens and antennae.
Related posts
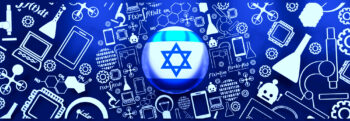
Israeli Medical Technologies That Could Change The World
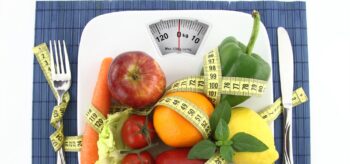
Harnessing Our Own Bodies For Side Effect-Free Weight Loss
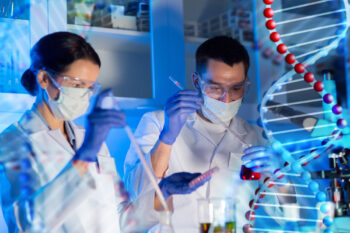
Missing Protein Could Unlock Treatment For Aggressive Lung Cancer
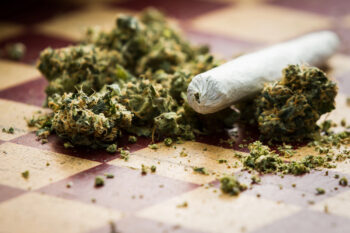
Facebook comments