Three-dimensional technology is not new to the fashion world, as designers have experimented with 3D printers in recent years to create imaginative, high-fashion garments, but could the printers soon be replaced with a 3D pen originally conceived as a children’s toy?
Israeli textile designer Eden Saadon used precisely that “toy” – a 3D printing pen called the 3Doodler, currently retailing for under $50 on Amazon – as a design tool to create an entire collection of couture-style lace undergarments. The Shenkar design school graduate is credited with challenging traditional design techniques and taking fashion innovation to new depths, creating “fashion art” with intricate hand-tracings.
The lacy lingerie collection (created with black Flexy plastic, which comes with the pen), which include “delicate and volumetric lace items, based on classic textile design imagery (flora and fauna),” according to Saadon, has already earned her much acclaim, but the textile designer continues to call attention to the 3D design implement because of its eco-friendly, cost-effective and innovative nature.
“Innovation is something very important to me,” Saadon tells NoCamels, referencing the late Israeli president Shimon Peres’s oft-repeated sentiment that Jews and Israelis look for ways to make positive changes because they aren’t satisfied with the status quo. “The greatest contribution of Jews to the world is ‘dissatisfaction’ because it is the source of creativity,” he once said.
Saadon says she wants “to be a part of the amazing things happening here in Israel. I’m always looking around to see what we already have in our world in order to work it into my process.”
Engineering and design
Saadon didn’t start off as a designer. She was more focused on engineering and tech and almost studied electrical engineering at the Technion-Israel Institute of Technology. But a style tour with her mother that included a behind-the-scenes look at the Tel Aviv fashion world convinced her she wanted to move into textiles and she enrolled at the prestigious Shenkar College of Engineering, Design, and Art in Ramat Gan where she majored in weaving. It wasn’t until her fourth year at the distinguished design school that she realized engineering and design are quite similar and can go hand in hand.
SEE ALSO: The Future of Food? How New Israeli Tech Could Have You Eating Meals Made By A 3D Printer
Saadon says she happened upon the 3Doodler as she was working out what to do her final graduation project. She came across an Internet commercial featuring a child drawing a 3-dimensional model of the Eiffel Tower using the 3D pen. After learning how to produce fabric structures made of yarn using intricate weaving, knitting, and flatting techniques, the simplicity of the pen struck her, she says, and she ordered one.
Saadon’s first garment was a bra, she reveals, because even if she didn’t know at first what she was making, she felt it was easier to test her capabilities on a smaller garment that could be fully functional.
She eventually created her entire final project, 3DLace, a line of feminine lace undergarment items hand-made with yarn, using this 3D printing technique.
The process
The process of creating a handmade, one-of-a-kind haute couture piece can be painstaking and time-consuming, though Saadon says she likes the detail of it. “You need a lot of patience,” she explains, noting that she can spend as much as 10 hours a day in the studio working on her garments. “You need to know what to do, how to paint, so you don’t make mistakes. I did a lot of experimenting to understand what parts need to be more flexible.”
Initially dissatisfied with the thin polymer plastic, Flexy, that comes with the pen – which looks like a cross between a thick marker and a portable glue gun – Saadon experimented polymers called PLA and ABS, known in the field of 3D printing, to find material that would maintain functionality and shape, but still be somewhat flexible. She only realized that the Flexy was the best plastic for her creations with further experimentation. It allowed her to produce surfaces having textile qualities like draping, movement, flexibility, and lightness, even while drawing a 3D structure of varying density.
Saadon says she never really knows what she is creating until she is well into the process. “I start to design with materials and work with my hand before deciding what I will actually make — a dress, an accessory, a piece of clothing. The potential comes with my experimentation with plastic. There are no stitches so the garments are custom made based on Saadon’s personalization or a buyer’s interest.
Sign up for our free weekly newsletter
SubscribeHer lingerie collection includes floral shapes of plastic and materials that form webbing when draped over the body. Some are attached to nude tulle and mesh.
She has also designed dresses with fish scales and fishtails to test the dense parts and loose parts of the fabric. According to Saadon, the fish tails fall away from the surface under the force of gravity due to the fabric’s more dense nature.
Presenting her projects to the world
Saadon was in New York earlier this year to showcase her 3D designs at New York Fashion Tech Week and participate in New York Textile Month. In August, she was invited to present her work at the “Internet of Fashion” Meetup group on 5th Ave Microsoft store in Manhattan. Surprising her at the talk was Maxwell Bogue, the CEO of 3Doodler, who presented her with a 3D pen and invited her to the company offices.
According to Saadon, Bogue said his team at WobbleWorks, the company that makes the 3Doodler, came up with the 3D pen when they were making designs for children in a 3D printer and wanted the kids to have an easier way to draw freely and make their own creations. Later, Saadon says, the 3Doodler team made modifications to the pen after receiving feedback from adults who were using it.
SEE ALSO: Israeli Design Student Prints Brilliant Collection At Home
While Saadon’s pieces are novel in their own way, 3Doodler is aware that other fashion designers and artists are using the 3D pen for their own undertakings. Australian designer Erica Gray used ABS plastic in combination with the 3Doodler to create wearable art with skeletal and animal imagery for her futuristic Forms Organic series. Rachel Goldsmith used the 3Doodler for a collection of lamps and other fine art that was displayed in Museum of Modern Art (MOMA) design store windows.
A model wearing Saadon’s 3D floral lace designs (Photos: Doron Sieradzki)
3D printer vs 3D pen
Saadon shrugs off any comparisons to two Israeli designers who have made names for themselves through fashion collections created with a 3D printer, Danit Peleg and Noa Raviv, also Shenkar graduates.
Peleg created the world’s first entirely 3D printed fashion collection for her final project and now has a customization platform on her website for customers to personalize and order their own 3D garments.
In 2014, Raviv created a 3D print collection by manipulating digital images using computer modeling software developed by Stratasys, an international leader in 3D printing with research and development facilities in Israel. Her work has also been displayed in the New York Metropolitan Museum of Art.
The biggest difference between Saadon and the two designers, Saadon explains, is that their work is computer-based. “I’m using tech but it’s the tool that I use. I work with my hands. I draw everything. They can repeat the designs that they do. The things that I’ve done, I can’t repeat them. They are more couture and handmade,” she explains.
Following the success of her 3D lace collection, Saadon is now experimenting with new fabrics for different shapes and occasions, creating new flexible haute couture for bridalwear, swimwear, and shoes. She is also experimenting with the more advanced 3Doodler Pro, which can draw in metal, wood, nylon, and polycarbonate.
Related posts
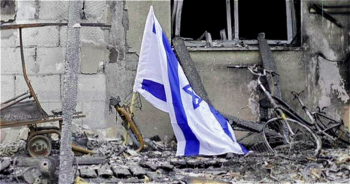
Rehabilitation Nation: Israeli Innovation On Road To Healing
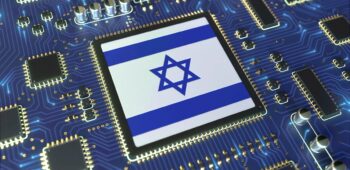
Israeli High-Tech Sector 'Still Good' Despite Year Of War
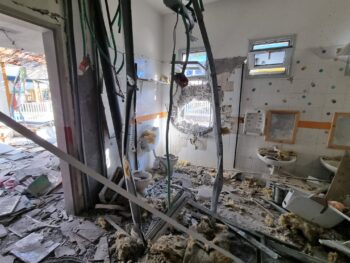
Facebook comments