McDonald’s restaurants in Brazil are rolling out serving trays across the country made with UBQ Materials’s waste conversion technology to replace the food giant’s plastic trays with a more sustainable version.
UBQ, the Israeli developer of a patented process to convert unsorted household waste into a fully recyclable thermoplastic substitute, made the announcement on Monday and said it would eventually supply some 18,000 sustainable trays in the coming weeks.
The partnership with Arcos Dorados (or Golden Arches), the largest independent McDonald’s franchisee in the world – which operates the brand in Latin America and the Caribbean – was first announced in late 2019.
SEE ALSO: Israel’s UBQ Materials To Set Up Waste Conversion Plant In Netherlands
The new trays are the first step in the partnership between Arcos Dorados and UBQ Materials, the companies said. In the initial phase, 7,200 serving trays made with UBQ were introduced in 30 McDonald’s restaurants in 20 Brazilian state capitals. The initiative will be gradually extended to all McDonald’s restaurants in Brazil with 11,000 additional trays already in production.
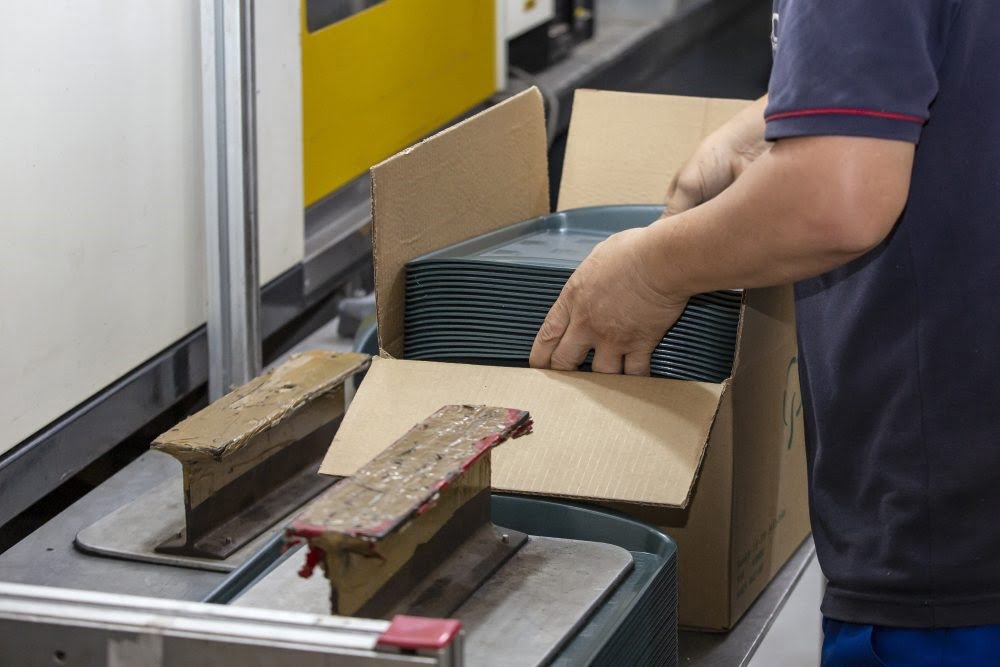
The trays are marked with the UBQ logo but patrons “will see and feel no difference in the iconic serving tray as the impact of this collaboration is in the intangible offset of carbon emissions,” the companies said in a statement. Some 1,200 kg of waste has been diverted from being sent to landfills as a result of the new initiative, UBQ indicated.
The measure is part of a multi-pronged plan by McDonald’s to reduce the use of plastic across its restaurants and operations.
Arcos Dorados said the implementation of the trays produced with the UBQ material complements a series of initiatives focused on reducing plastic use, including substituting some of the packaging on products and suspending the proactive use of plastic straws in its restaurants.
“The partnership with UBQ is yet another step towards introducing more and more innovative solutions to improve the world around us, and we are proud to take this first step, supporting a technology that will transform the way society recycles its organic waste,” said Gabriel Serber, Director of Sustainable Development and Social Impact at Arcos Dorados.
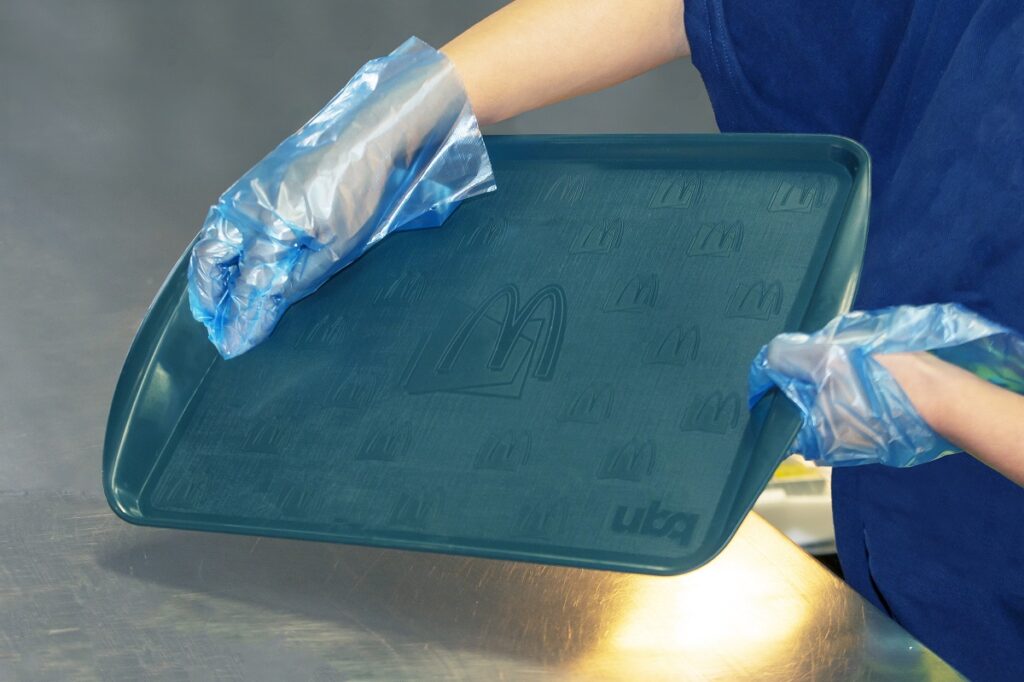
Albert Douer, executive chairman of UBQ Materials, said the company “has the potential to revolutionize the way we view waste, transforming it from a liability into a valuable resource for manufacturing.”
Sign up for our free weekly newsletter
Subscribe“The market at large is demanding sustainable solutions and the fast-food industry is no exception. UBQ enables manufacturers to create products that positively impact our world, without compromising on profitability – the solution is as simple as implementation,” he added.
UBQ’s solution
UBQ Materials was founded in 2012 by Rabbi Yehuda Pearl, a founder of the globally recognized hummus brand Sabra and Jack “Tato” Bigio, an entrepreneur in the renewable energy sector. The team emerged from stealth mode in late 2018.
The company, whose name is derived from the word “ubiquitous,” produces a patented material converted from 100 percent unsorted household waste, containing food leftovers, mixed plastics, paper, cardboard, packaging materials, and diapers. The unsorted waste stream is reduced to its most basic natural components and then reassembled and bound together into a matrix, creating a novel climate-positive material with applications across industries.
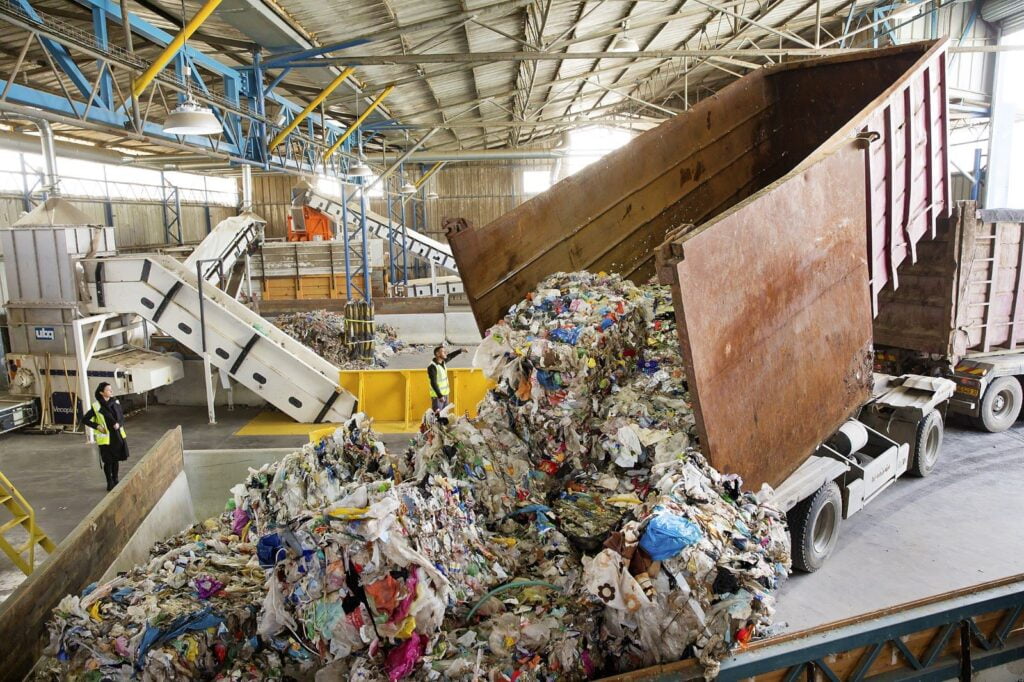
As a raw material, UBQ says that its products can be used in thousands of applications including shopping carts, pipes, trash cans, and automotive parts.
In the US, the Central Virginia Waste Management Authority (CVWMA) is using thousands of recycling bins made with UBQ’s converted waste material. And last year, the company announced a number of new opportunities, including a partnership with Daimler to test its solution for the production of “clean” automobile parts, a collaboration with Indian automotive company Motherson Group to implement UBQ’s carbon-negative thermoplastic in auto parts, and a pilot with global retail solutions provider Mainetti for sustainable garment hangers.
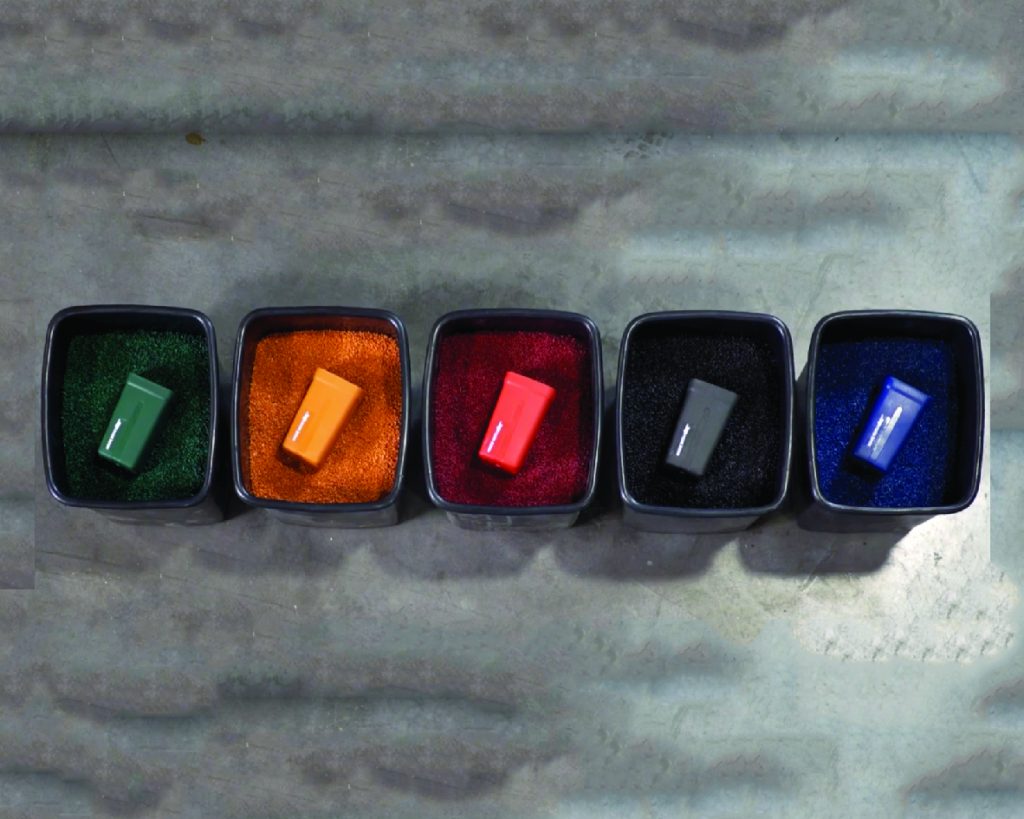
In an interview with NoCamels in 2019, Bigio said UBQ Materials provided a climate positive solution, which he said included an energy-efficient and environmentally sound process where no emissions are produced, no water utilized, and no waste left behind. It saves 11.7 kg of carbon dioxide equivalent emissions per kg. of UBQ produced, he explained at the time.
“We’re taking the waste before it goes to the landfill,” he said. “There’s no technology today that does that.”
UBQ has a plant in Kibbutz Tze’elim in southern Israel where some 7,000 tons of garbage is converted per year, and is set to establish a full-scale waste conversion plant in the Netherlands with plans to do so in the US as well.
Related posts
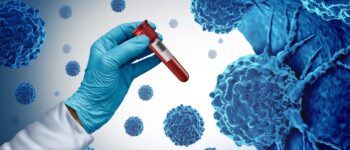
Editors’ & Readers’ Choice: 10 Favorite NoCamels Articles
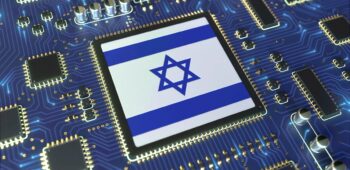
Forward Facing: What Does The Future Hold For Israeli High-Tech?
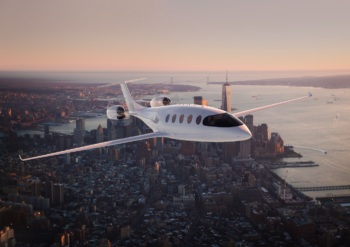
Impact Innovation: Israeli Startups That Could Shape Our Future
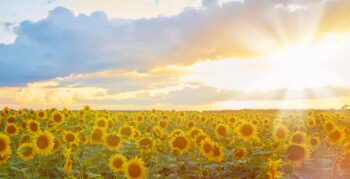
Facebook comments