The world produces approximately two billion tons of waste per year, a staggering figure that is expected to jump to more than three billion tons over the next 30 years, according to a recent report by the World Bank appropriately titled “What a Waste.”
Plastics are the most problematic, the report says. When not collected or managed properly, they contaminate waterways and ecosystems for years. In 2016 alone, the world generated 242 million tons of plastic waste, which accounts for 12 percent of all solid waste around the globe.
SEE ALSO: Israel Has A Severe Plastic Problem, But Real Change Is Possible
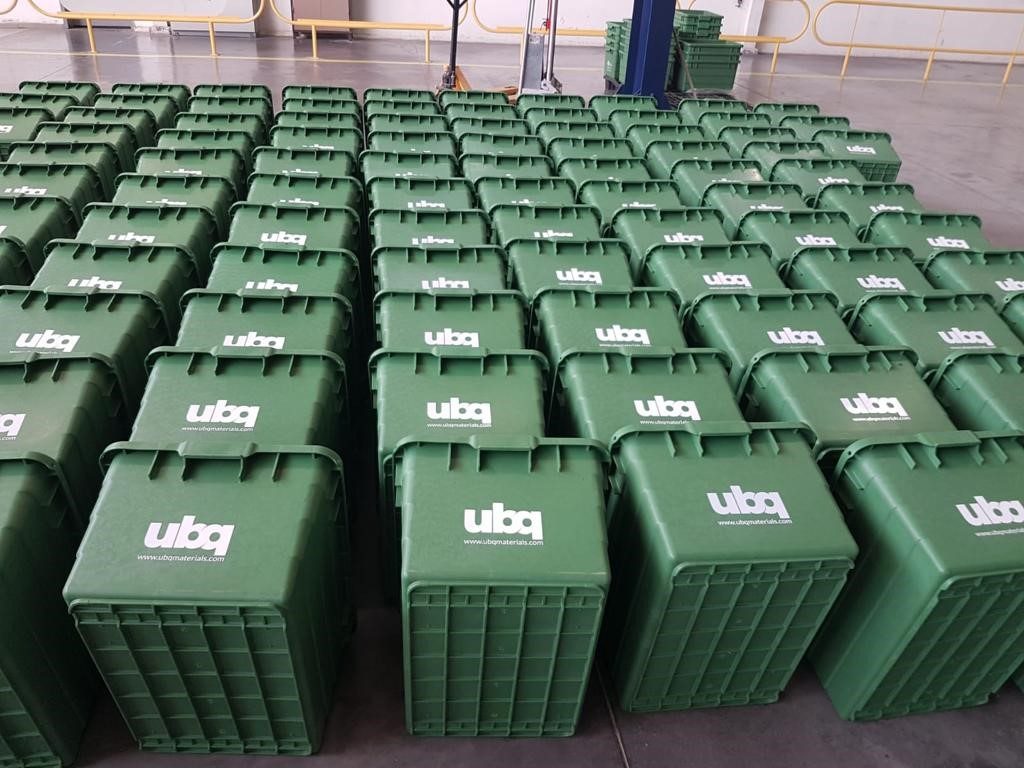
Supporting countries to reduce plastics, draft critical solid waste management policies and provide finances for waste removal is key, the World Bank says, and “good waste management systems are essential to building a circular economy, where products are designed and optimized for reuse and recycling.”
Israeli startup UBQ Materials had found a way to do just that. The company developed an innovative, patented process to convert unsorted household waste — think chicken bones, dirty diapers, hamburger leftovers, and yogurt containers — into a sustainable, fully recyclable thermoplastic substitute.
“We’re taking the waste before it goes to the landfill,” the company’s co-founder and CEO Jack “Tato” Bigio tells NoCamels. “There’s no technology today that does that.”
Bigio also calls UBQ Materials a climate positive solution, which he says is an energy-efficient and environmentally sound process where no emissions are produced, no water utilized, and no waste left behind. It saves 11.7 kg of carbon dioxide equivalent emissions per kg. of UBQ produced, he explains.
UBQ, derived from the word “ubiquitous,” has been “transforming waste into a new natural resource” in Israel, and now in the United States, Bigio says.
The revolutionary technology was recently adapted in a pilot program by the Central Virginia Waste Management Authority (CVWMA) which ordered the first 2,000 recycling bins made with UBQ Materials’ converted waste material.
The Virginian authority, which provides waste management and recycling services for thirteen local governments, including Richmond, Chesterfield, and Herico, is the first in the United States to use the solution developed by UBQ Materials.
At least 7,000 tons of garbage is converted at the UBQ plant in Kibbutz Tze’elim in southern Israel per year. The company hopes to expand internationally with additional locations in the US, Europe, and Asia. Bigio is mum on exact details, but says new plants are “in development.”
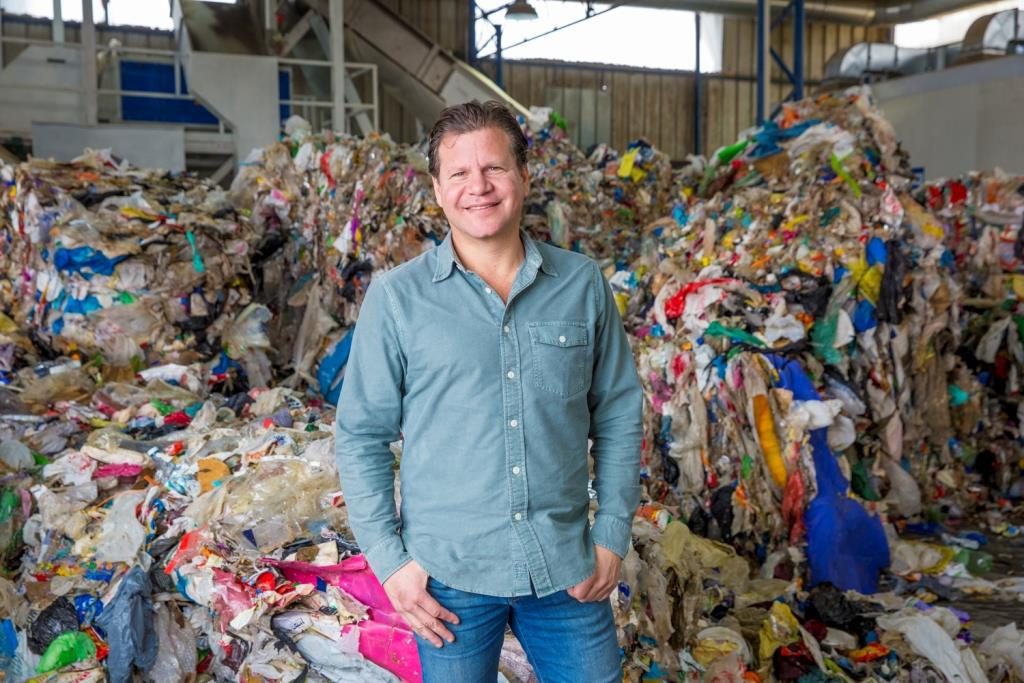
UBQ also has customers for its bio-based composite material both in Israel and abroad. The demand for sustainable and climate positive materials is significantly growing, says Bigio, who says manufacturers, retailers, brands, and international conglomerates have approached the company as they search for the best way to reduce their own company’s carbon footprint.
While Bigio is tight-lipped on UBQ’s customers in Israel, he does say that there are big plastic manufacturers and global brands among them, looking for an environmentally-friendly alternative to plastic.
The Virginia connection
UBQ Materials was founded in 2012 by Rabbi Yehuda Pearl, a founder of the globally recognized hummus brand Sabra and Bigio, an entrepreneur and leader in the renewable energy sector. The team emerged from stealth mode in late 2018.
Bigio admits that it took a while because they wanted to make sure every possible question was answered, validated and duly certified, and no one could say contradict the solution.
There were a few reasons that the company considers entering the US market through Virginia. The first is that one of the largest manufacturing plants for Sabra’s refrigerated dips product is located there. Naturally, Pearl had a good rapport with the local and state government in the region and made the connection.
The second reason is that Virginia is home to roughly 60 landfills, including eight mega-landfills (that can accept more than 3,500 tons of waste per day.) New York and Pennsylvania also send their waste to Virginia, according to Bigio.
Sign up for our free weekly newsletter
Subscribe“The locals are not happy. Landfills are very contaminated places. We’re in the right place at the right time,” he adds.
“I am sure that this partnership will lead to great opportunities for UBQ and our partners, just as I am sure that it will create a better future and a cleaner world,” Pearl said in a statement announcing the pilot in Virginia.
UBQ Materials has high-level backers. The company’s international advisory board is a smattering of high-level educators, and scientists including Nobel Prize Winner Professor Roger Kornberg, nanotech pioneer Prof. Oded Shoseyov, patent practitioner Dr. Ilan Cohen, and John Elkington, a world authority on corporate responsibility and sustainable development. There’s also Connie Hedegaard, the European Commissioner for Climate Action, whom Bigio says is highly impressed with the company’s circular approach and its technology.
Can UBQ help solve the world’s plastic problem?
In June, the coast of Tel Aviv was ranked third highest for plastic waste on its shores in a report from the World Wildlife Fund for Nature which looked at the most plastic polluted areas of the region and ranked the city among 22 countries in the Mediterranean.
The report said Tel Aviv is a “hotspot” for about 21 kilograms (46 pounds) of daily plastic debris accumulation on the coastline. It ranks third after Turkey’s Cilicia region which has 31.3 kilograms (69 pounds) per kilometer and Barcelona, which has 26.1 kilograms (58 pounds) per kilometer. The Po Delta region of Italy comes in fourth behind Tel Aviv with 18.2 kilograms (40 pounds) of plastic waste per kilometer.
The country with the highest amount of plastic waste that is not disposed of properly is Egypt (42 percent of all waste), followed by Turkey (18.9 percent) and Italy (7.5 percent).
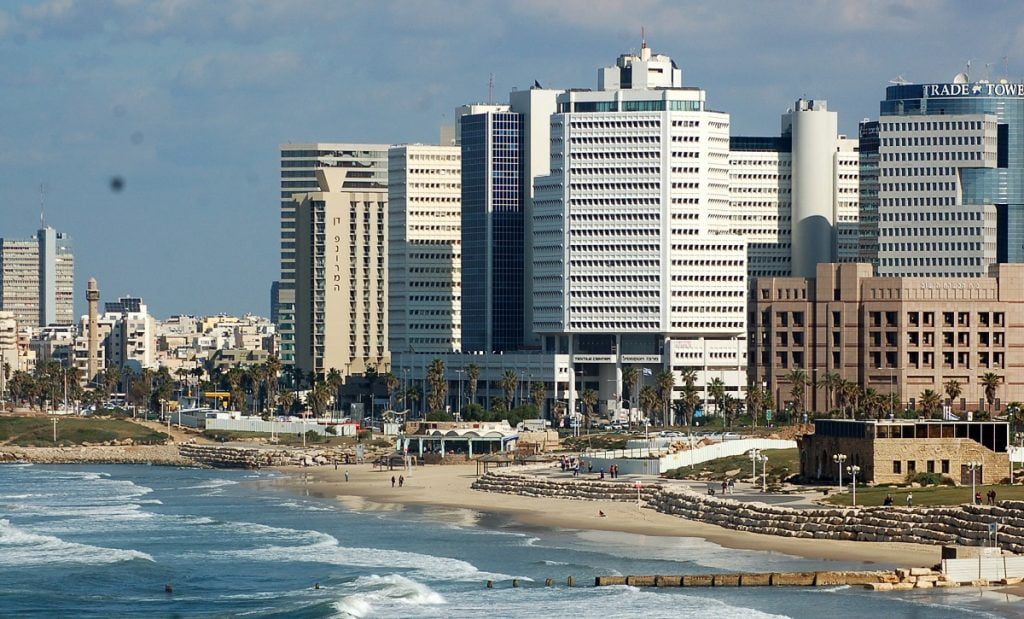
According to the report, the Mediterranean region is the world’s fourth-largest producer of plastic goods, producing 10 percent of all plastic products, the World Wildlife Fund said. Inhabitants of the region generate about 24 million tons of plastic waste each year.
“Plastic has become a ubiquitous material in the Mediterranean,” the report’s opening paragraph reads. “Every year, 0.57 million tons of plastic enters Mediterranean waters. This is equivalent to dumping 33,800 plastic bottles into the sea every minute. Without action, this number will keep growing as a plastic waste generation in the region is expected to quadruple by 2050. “
Bigio says the world’s plastic problem is exactly why UBQ Materials was created in the first place. “Plastic is a great material. It allows us to create products that are lighter and stronger, which is extremely efficient. The problem is once you throw it away, you need a system to recollect and recycle it.”
The system to separate the plastic, he explains, is a cumbersome and expensive process. Landfills become too full and the plastic ends up in the ocean or other bodies of water (hence, a good explanation for the large amounts of plastic in our rivers and oceans.)
SEE ALSO: Israeli Researchers Produce Sustainable Bioplastics With Seawater Algae
UBQ Materials says it tackles this issue before it becomes a problem. “We don’t need to separate anything,” Bigio says, “We just take the plastics together with the food waste, the cardboard, and paper and convert it into a new climate positive material. This new material can be used by the existing manufacturing industry again and again and recycled many times. It’s an easy way to dispose of the plastic and ease the process through a commercially viable solution.”
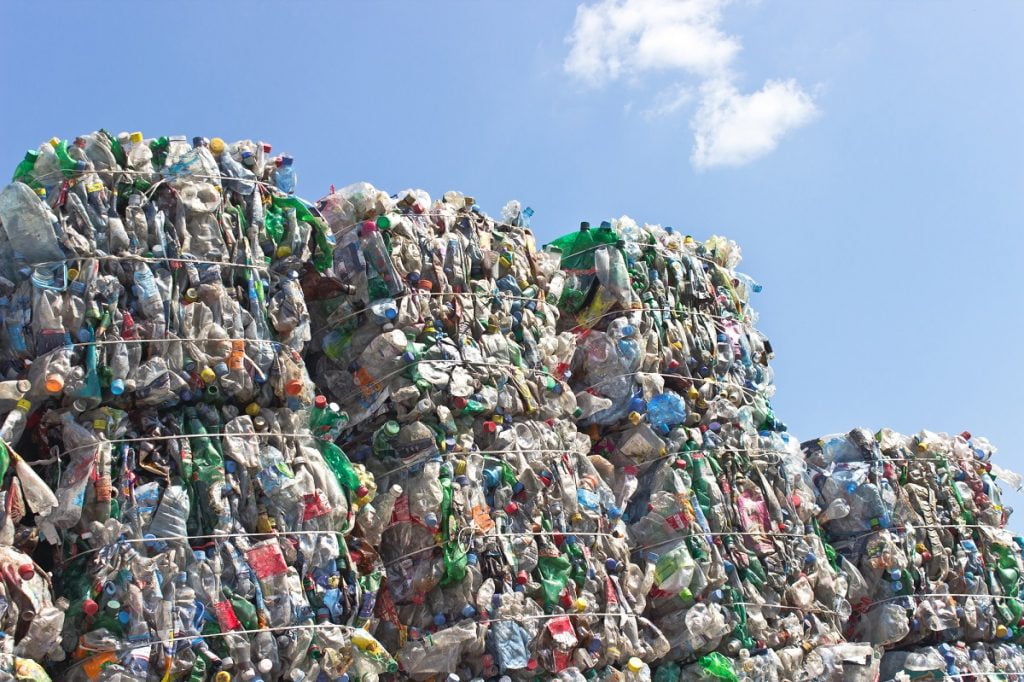
So will it tackle the problem in Israel? UBQ Materials strives to do it everywhere, Bigio says, though he admits there is much more interest abroad than in Israel because of more environmental awareness.
“Europe, USA, Canada, Australia, Japan are much more conscious than us [Israel], Bigio says, but “Israel is catching up.”
While Bigio calls UBQ Materials a “plastic replacement company,” he also adds that the converted waste can be used in the construction industry to make bricks, pavement, buildings and more. But currently, he indicates, the focus of the company is in the plastics business.
The company continues to find new applications for the solution. In the meantime, it continues to gain international recognition, snapping up awards like the “Best Use of Alternative Feedstocks” here at the Bio Market Insights Conference in May and the Leadership in Innovation Award at the Re|focus Sustainability & Recycling Summit hosted in Grand Rapids, Michigan in June.
Related posts
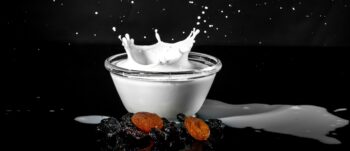
Resilient And Nutritious New Plant-Based Milk Aims To Make A Splash
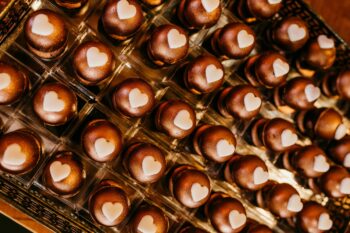
Chocolate From Cultivated Cocoa Comes Without Environmental Toll
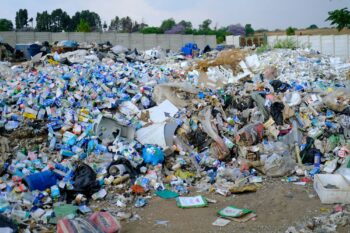
Plastic Fantastic: Startup Takes PVC Back To Its Crude Oil Roots
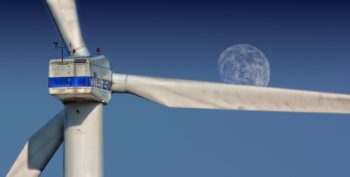
Facebook comments