Emissions can be used in the food, animal feed, fertilizer, and glass industries
Thick, polluting smoke from factory chimneys is a “necessary evil”, but what if it could be turned into something valuable instead?
A startup in Israel is doing exactly that, with a new carbon capture technique that transforms the emissions into profitable minerals, instead of securing it underground like conventional technologies.
It’s a win-win solution, because the process releases zero carbon emissions – and it generates a useful commodity.
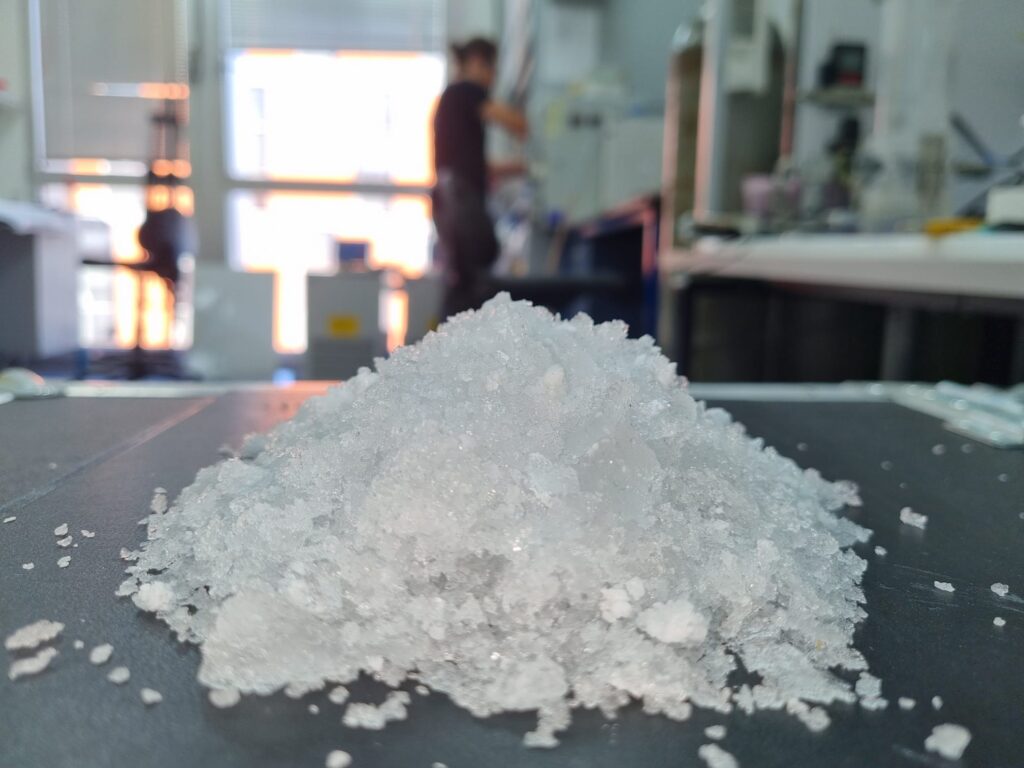
Reactors are connected to the smokestacks to stop the pollutants from ever being released into the environment.
The polluting gasses pass directly through the reactors, and bind to unstable components to create minerals that can be used in the food, animal feed, glass and fertilizer industries.
Airovation Technologies, the company that developed the technique, can turn one tonne of carbon dioxide a day into minerals. By 2024 it expects to “mineralize” 15 tonnes a day, in a single plant.
“The idea is simple: we take carbon emissions, and use the carbon itself as a feedstock,” says Marat Maayan, CEO and Co-founder of the company.
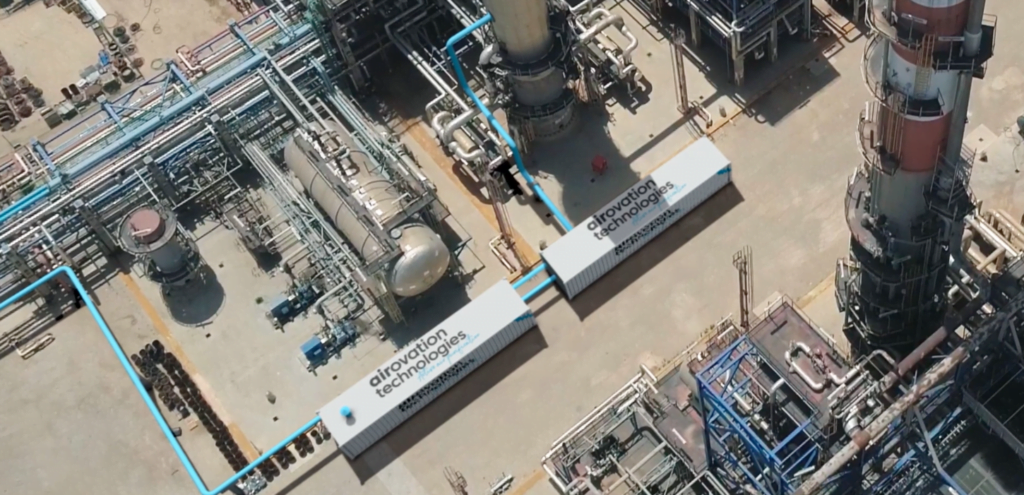
“We help factories become zero-carbon emitters. Especially those that are really struggling to shift to zero carbon, like the glass industry, which generates emissions from the raw materials that they are melting.”
Airovation collaborates with its partners, building sites near their factories that can turn polluting carbon emissions into sodium carbonate and bicarbonate, and potassium carbonate and bicarbonate.
The companies simply go about their industrial processes, but instead of releasing their carbon emissions into the air, the bottom of their chimneys directly pumps them into diffusers within the on-site reactors.
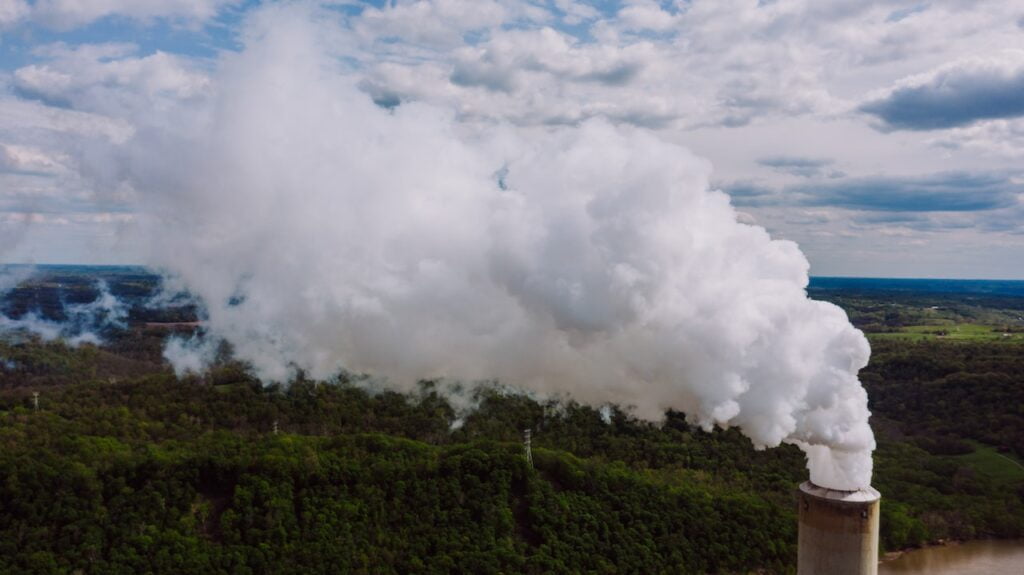
The main input the technology needs is a liquid, alkaline-based product, which Airovation buys from local manufacturers.
Its reactors add a catalyst to this liquid solution, which generates oxygen molecules with unpaired electrons, known as ‘superoxide radicals’.
The unpaired electrons – or radicals – make the oxygen molecules very unstable, and results in them instantly reacting with the carbon dioxide-filled smoke that passes through the reactor, solidifying the carbon and turning it into valuable materials.
“We have this very unique, very fast reaction of mineralization. So we’re doing capturing and storage in some sense, inside the material.
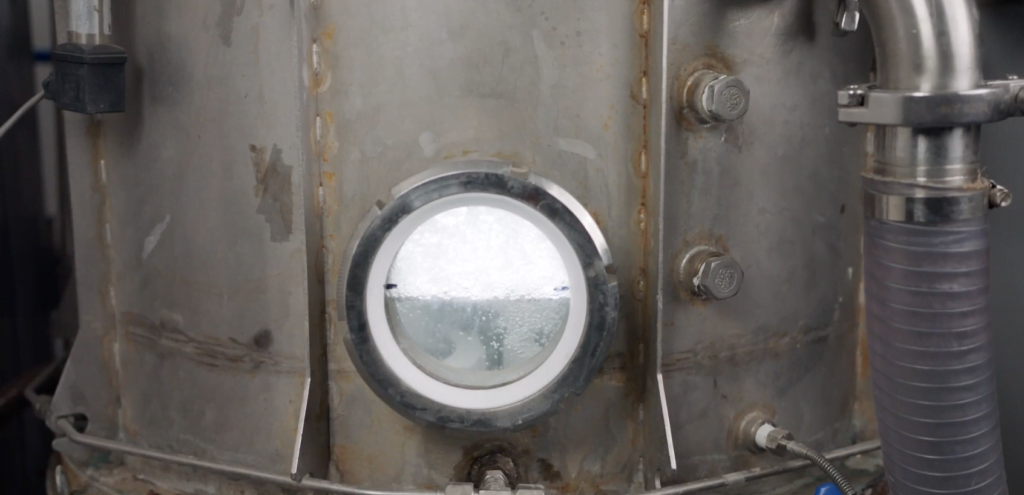
“And this material can be used. It can be manufactured in a variety of ways, from point sources to post-combustion processes, and can support different industries that today have a very hard time to move to zero-carbon, for example, the glass industry.”
Businesses, particularly in Europe, receive a certain number of ‘carbon credits’ every year, each one representing the right to emit emissions equivalent to one tonne of carbon dioxide.
Those that can’t easily reduce their emissions operate at a higher financial cost, or can buy credits from companies that do not need theirs. Carbon credits create a monetary incentive for companies to reduce their carbon footprints.
Sign up for our free weekly newsletter
SubscribeMaayan gives an example of one of its partners, a European glass factory, which has to pay around 100 euros ($106) for each tonne of carbon dioxide it emits.
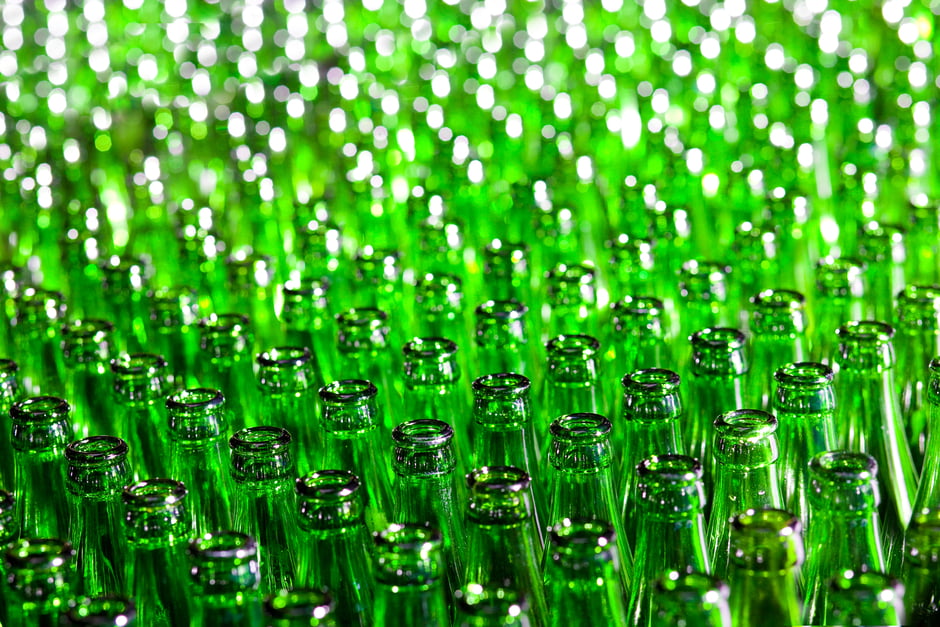
“Now, we’re not only managing to bring in zero carbon emissions on their site and help them save millions of euros in penalties a year,” he says, “but we are also able to supply them with minerals that have a neutral carbon footprint for a lower price.”
This factory uses truckloads of sodium carbonate every day. The material normally needs to be manufactured in Europe, and shipped to the factory, but Airovation brings stability to the supply chain, in addition to preventing further carbon emissions.
“Last year, the supply chain [of sodium carbonate] was crazy,” he says. “And the prices of shipping things, and getting those shipments on time, was very sensitive.”
Now, factories that partner with Airovation will not need to exclusively use outside sources, but will also have a steady supply – being produced in their own backyard.
And it’s more cost-effective than relying solely on outside shipments. This is in addition to the carbon credit penalties that the factories would be avoiding.
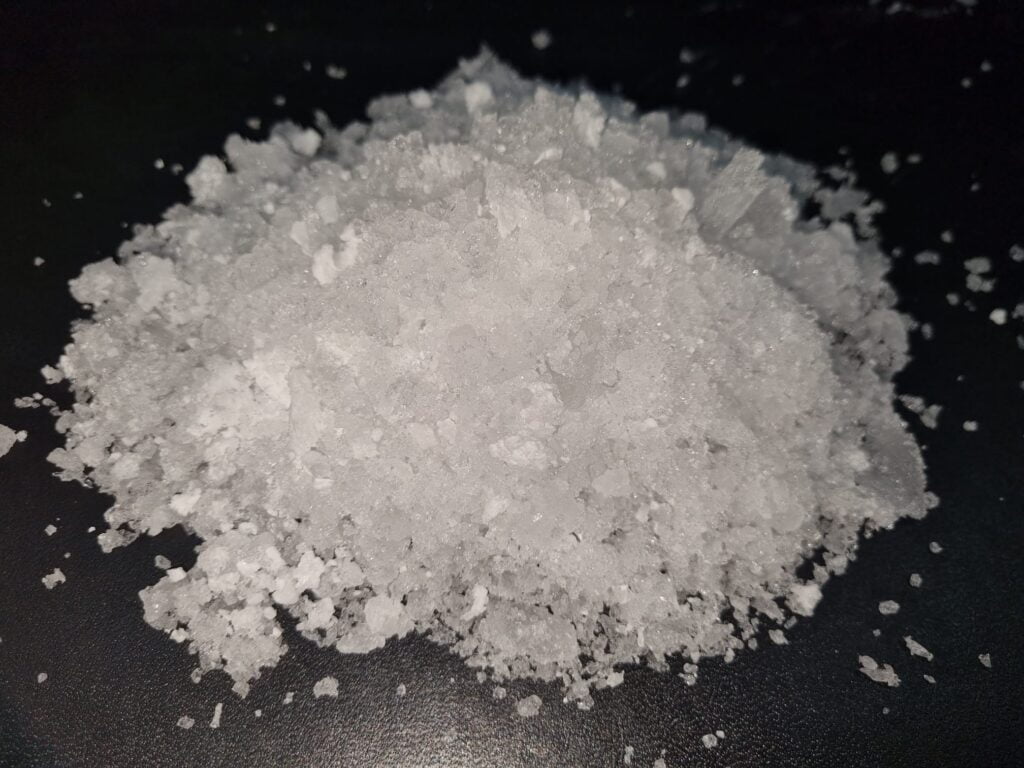
Creating sodium carbonate and bicarbonate, and potassium carbonate and bicarbonate is a very energy-consuming process, and in some cases, mining is involved as well.
These factories would be buying the product from Airovation, after producing it on-site.
“The idea is to have a long-term contract of local supplies, and create a circular economy.”
The first factory that is scaling up with its mineralization technology is Phoenicia, an Israeli glass manufacturer.
But because there are no carbon penalties in Israel, Airovation is primarily focusing on European and Asian countries.
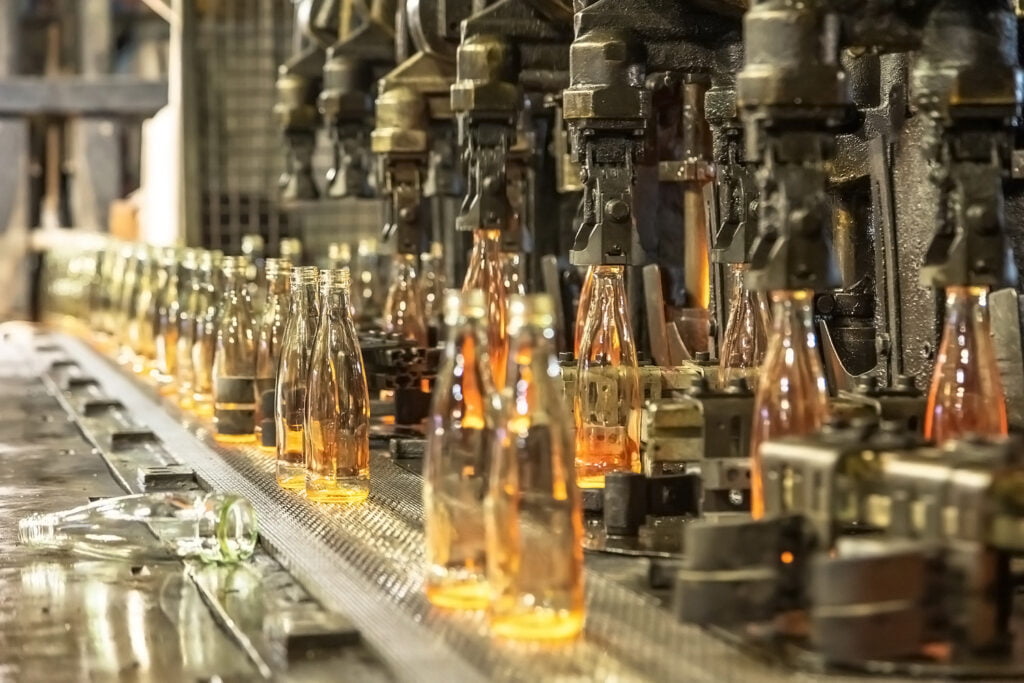
In South Korea, it is partnering with Kolon Industries, a chemical and textile manufacturing company. It is also working with Unid, another South Korean firm that manufactures 35 per cent of the global manufacturing of potassium hydroxide, a disinfectant.
Traditional carbon capture technologies, known as direct air capture (DAC), extract carbon dioxide directly from the atmosphere, and either store it deep underground, use it in beverage carbonation or food processing, or combine it with hydrogen to produce synthetic fuels.
But it is very energy intensive and expensive to do so. Maayan doesn’t see these companies as competitors, but as partners.
“It’s very easy to be in love with what you invented,” he says. “But to create a really big impact, you have to collaborate with others and you have to create a kind of a toolbox approach. We’re not a ‘silver bullet’ – our technology is just a piece of a puzzle.”
Related posts
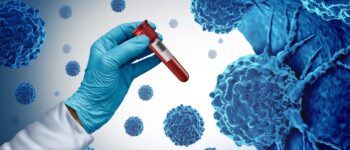
Editors’ & Readers’ Choice: 10 Favorite NoCamels Articles
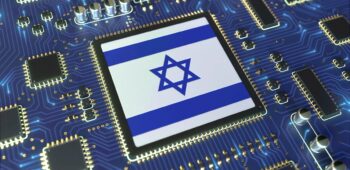
Forward Facing: What Does The Future Hold For Israeli High-Tech?
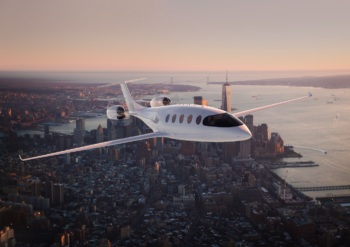
Impact Innovation: Israeli Startups That Could Shape Our Future
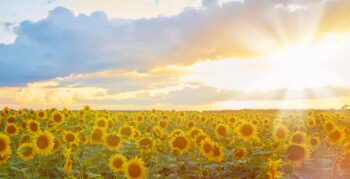
Facebook comments