Prof’s sustainable plan to compress mountains of waste into “new cement”
We have too much salt. There are literally mountains of it, and they’re growing bigger day by day, hour by hour. A small proportion of the world’s salt is used for food. But the vast majority of it is a waste product, left over after desalination plants have made sea water drinkable, or after heavy industries have extracted potash – soluble forms of potassium – from it for fertilizers.
Daniel Mandler, professor of chemistry at The Hebrew University of Jerusalem, wants to turn it into bricks, in what could be a massive win-win for the planet. He’d be turning a worthless pollutant into a strong and valuable building material, and he’d be making a dent in the cement industry’s enormous carbon footprint.
He’s already produced prototype bricks in his lab. He adds a patented mix of ingredients to prevent the salt dissolving, grinds it, and compresses it into a brick that’s many times stronger than cement.
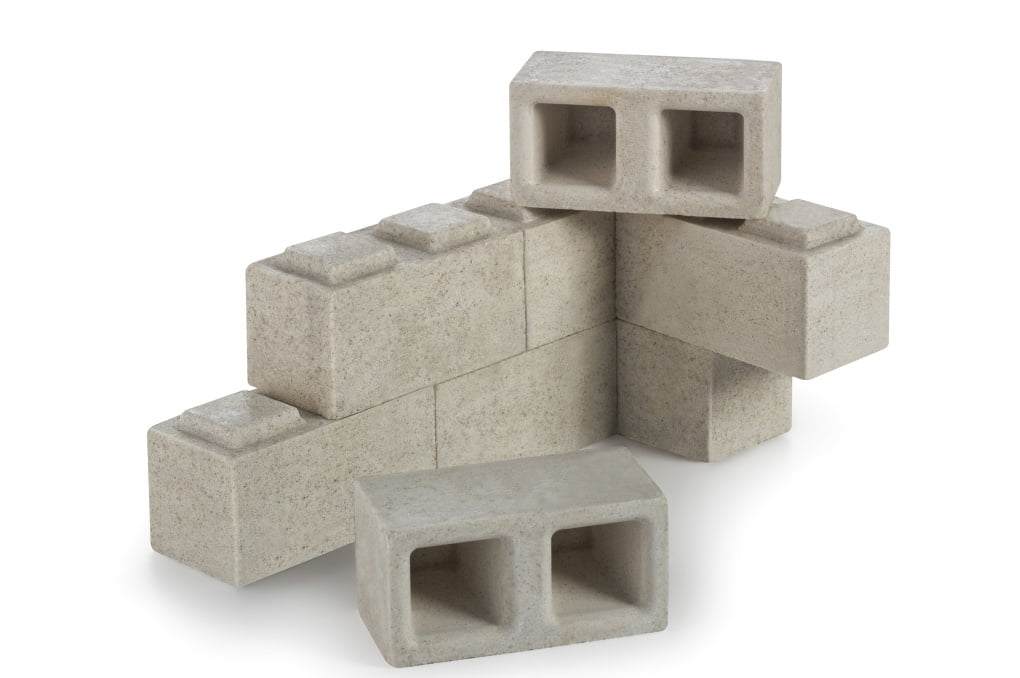
There are many technical challenges still to address and much inertia to overcome in a building industry that is slow to embrace new ideas, he says. But Prof Mandler is convinced that salt – the basic ingredient we add to our food – could become the building material of the future.
“There’s still a long way to go,” he tells NoCamels. “I don’t have a final product and that’s why I’m trying very hard to raise some funds to go to the next step and to carry out a pilot and then to actually build the first building made of salt.”
Consider two things for a moment – the amount of salt piling up across the globe, and the damage being done by cement production – and you’ll see what makes salt bricks such an attractive proposition.
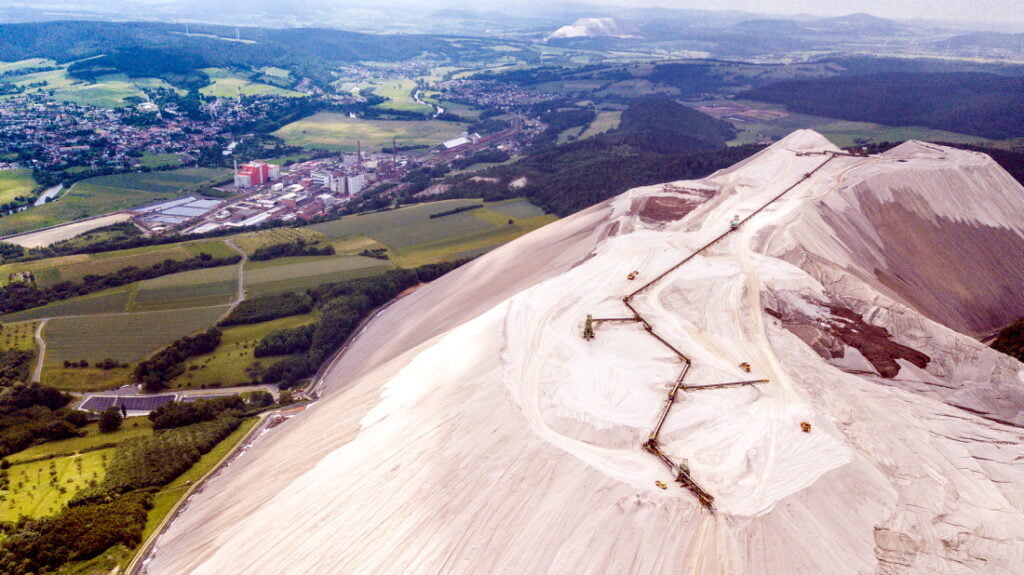
In Germany there’s a 650ft high mountain, called Monte Kali, made entirely of salt. K+S, Europe’s largest producer of potash for fertilizer, adds another 900 tonnes of salt every hour. The salt mountain is a tourist attraction, with thousands of visitors scaling its heights every year.
But the 200 million tonnes of salt are seeping into the ground, polluting the soil, rivers, and groundwater. It’s a similar picture in Belarus, where you can book a tour of the 300ft high salt mountains that give their name to the city of Soligorsk, the legacy of 70 years of potash mining.
On the border between Israel and Jordan, salt from the Dead Sea, the lowest point on Earth, is evaporated in vast pools to produce potash. On the Israeli side alone that yields 20 million tonnes a year of salt that nobody wants.
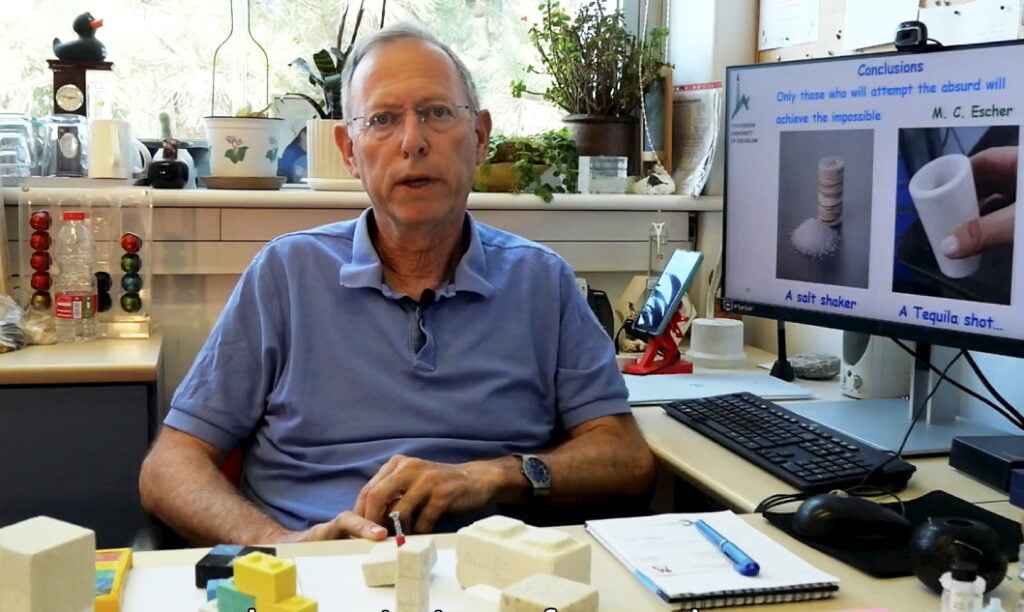
Now consider cement production. It is, says Prof Mandler, one of the most polluting industries in the world, directly responsible for between eight and nine per cent of carbon dioxide emissions globally. Manufacturers heat calcium carbonate to 1,500 degrees Celsius, releasing vast amounts of carbon dioxide in the process, and consuming vast amounts of energy.
Salt bricks are a simple, sustainable, but so far unfunded solution, killing two birds with one stone. They offer clear and compelling advantages. But they are untried and untested. And Prof Mandler has yet to find the backers and funders to turn them into reality.
The process of making them is remarkably straightforward. “We make a mold out of stainless steel,” he says. “And in a very, very simple process at room temperature, we mix the salt from the Dead Sea with about five per cent of different ingredients, then we grind them and then we compress them with about two tonnes per square centimeter of pressure.
Sign up for our free weekly newsletter
Subscribe“And that’s it. It’s ready. Nothing else. If you compare that for example, to cement, the carbon footprint here is almost zero.”
So far the size of brick he’s made has been limited by the equipment he has. The next step is to build a wall of salt bricks, then an entire building, so he can fully test the bricks’ properties.
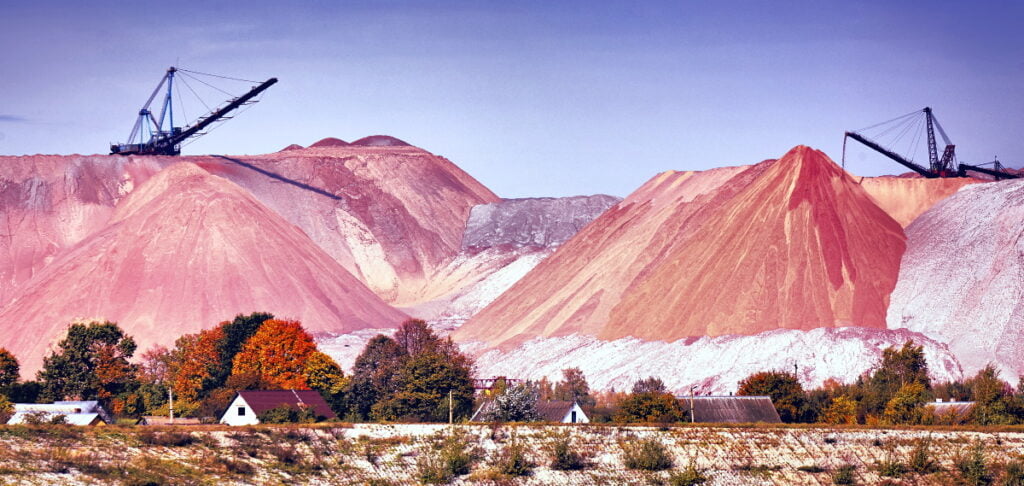
“When we started actually working on the research, people thought it was so crazy that I didn’t even dare to ask for some support,” he says.
“I’m so busy. I have 20 students in my research group, and I don’t have the time to spend totally on this project. So I need somebody who will believe in this project. We’ll raise some funding and then we’ll go to the next step to produce bigger bricks.
Early on in the research he received NIS 800,000 ($235,000) from Israel’s Ministry of Innovation. He’s now waiting to hear if it will provide additional funding, and he’s also approaching other sources.
“We need to raise funding from either a governmental office or from a non-profit agency that will believe in what we do, and will support us,” he says.
He is working with Yissum, the university’s tech transfer body that helps bring innovation out of the lab and into the marketplace. He believes companies able to commercialize the idea will want to see proof of concept – a small room or structure made entirely of salt – before they commit to the idea financially.
He’s upfront about the challenges he still faces. Solubility remains an issue. He’s been able to partially resolve the problem, but says there’s more work to be done. Also, salt corrodes metal, which is widely used in the construction industry. He doesn’t yet have a solution for that. And there are issues about density and flexibility, which also need to be tackled.
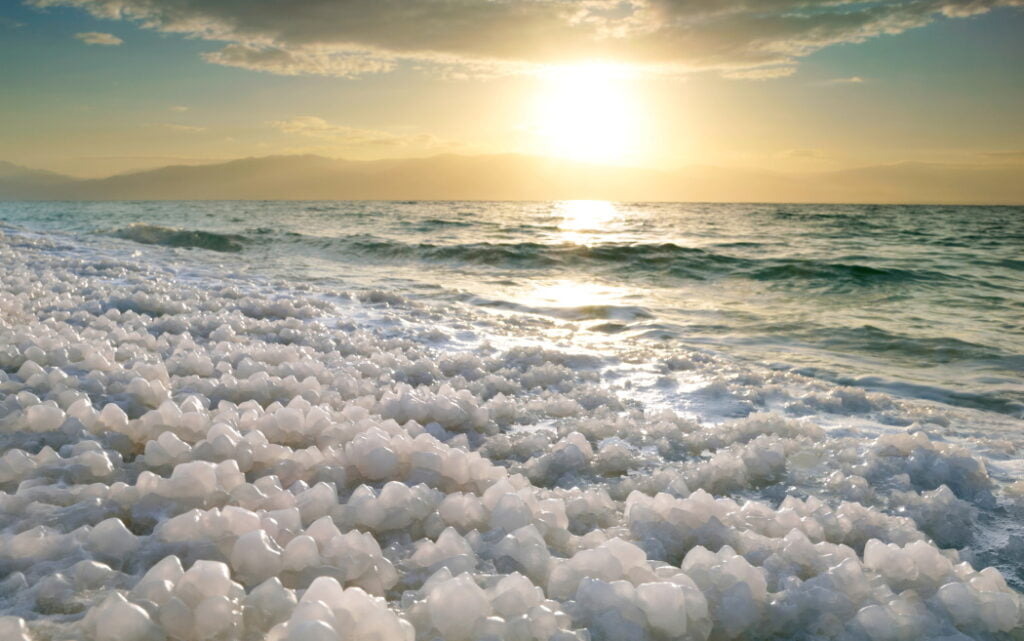
On the plus side though, salt as a building material is very sustainable, non-toxic, non-flammable, very strong, a good insulator, recyclable and antibacterial. Would it be cheaper than cement? Hard to say. Today the owner of a salt mountain would probably pay you money to take it off their hands. Tomorrow, if salt becomes a commodity for a new brick industry, things would probably change.
Is he frustrated that a great idea hasn’t yet achieved traction? “No, no, no, no. I’m optimistic,” he says. He has as a guiding principle the saying attributed both to Albert Einstein and the graphic artist MC Escher: “Only those who will attempt the absurd will achieve the impossible.”
Prof Mandler says: “You don’t do research unless you’re optimistic, because most of the things that we try don’t work.” Salt bricks may prove to be exception.
Related posts
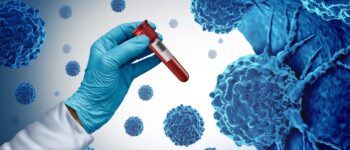
Editors’ & Readers’ Choice: 10 Favorite NoCamels Articles
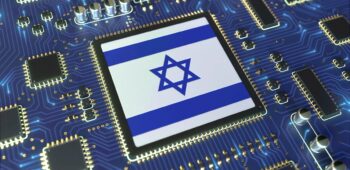
Forward Facing: What Does The Future Hold For Israeli High-Tech?
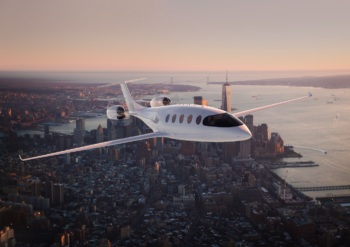
Impact Innovation: Israeli Startups That Could Shape Our Future
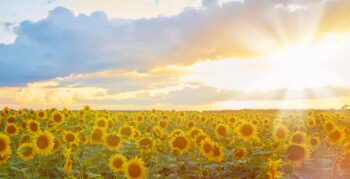
Facebook comments