Israeli startup turns waste from sawmills into a super-strong material
Wood waste is literally being molded like putty to create an array of household products.
It’s a healthy alternative to MDF (medium-density fibreboards), the mixture of wood fibers, toxic resins and wax that is used to create cheap wooden products – like the cabinets and desks sold by IKEA.
Daika Wood, the Israeli company behind the innovation, uses a special process to mix wood waste from sawmills with water and other natural ingredients like cellulose, and lignin, the material that makes wood rigid materials.
The all-natural material is already being used to create tabletops and wall coverings for office furniture company Steelcase, as well as screwdriver handles for Stanley Black & Decker, the world’s largest tool company. And the possibilities are endless.
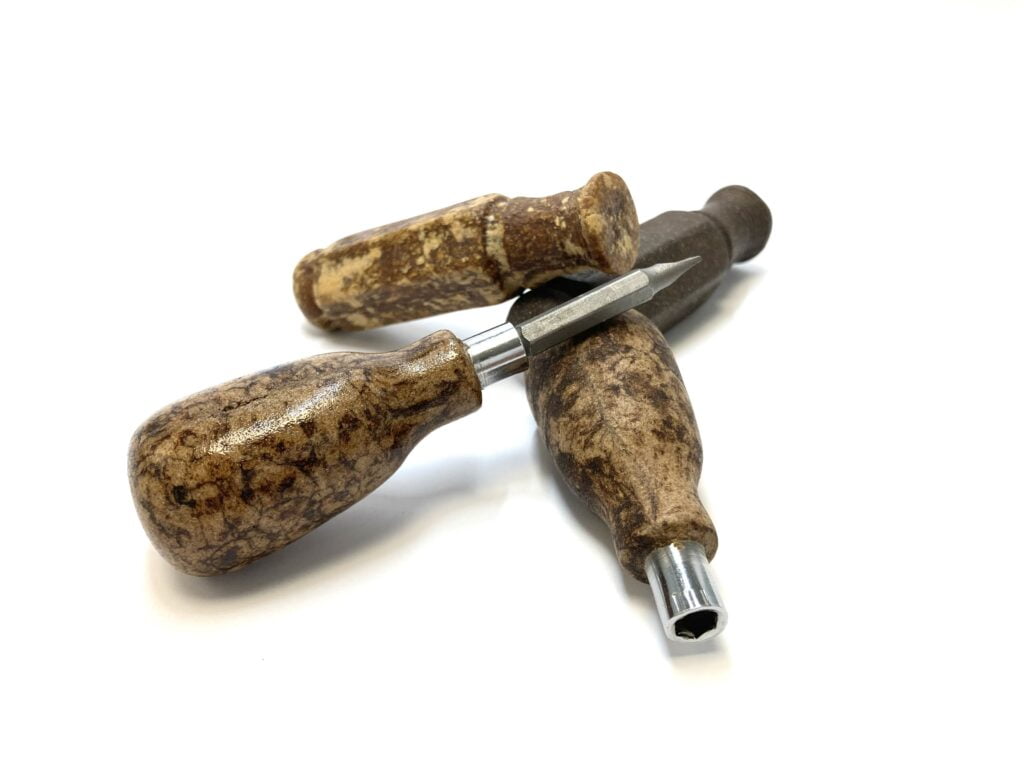
“This is an opportunity for companies to offer their consumers something that is natural, and looks and feels like real material,” says Dr Michael Layani, Co-founder and CEO of Daika.
“Across the board, consumers are gravitating towards more natural products.
“We take only natural ingredients, nothing coming from the petroleum industry. Our material is like plastic – it can flow and be molded into different shapes. Once it hardens you get physical properties that can compete with existing materials in the market.
“We take wood chips that are ground into flour and use water, and other natural ingredients, and what we get is something like Play-Doh,” he tells NoCamels. “You can shape it, and then it hardens and becomes very rigid.
“With Daika, it’s the best of both worlds. You can mold it to become any shape like plastic, and the end result still has the same properties as a fully-wooden object.”
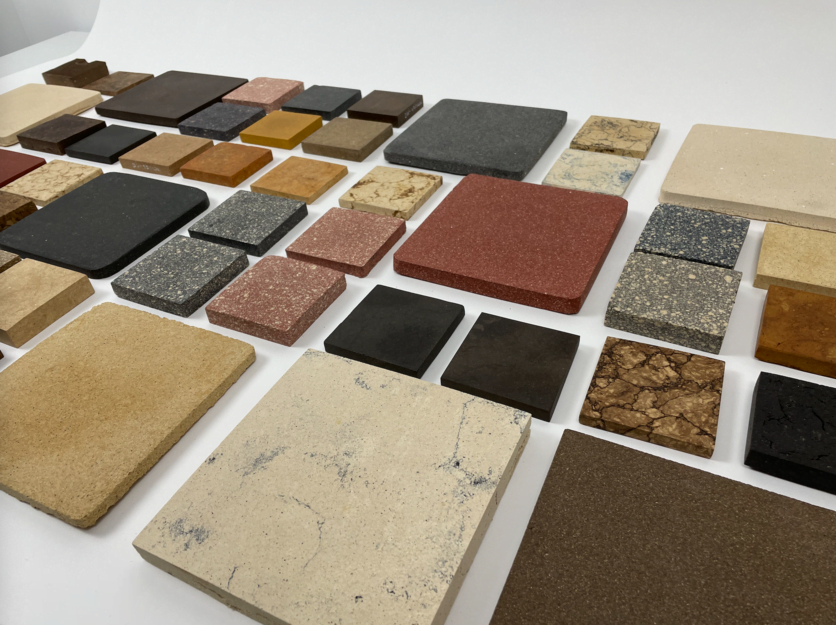
The company was founded through the Hebrew University of Jerusalem’s tech transfer company Yissum, after researchers there, including PhD student Doron Kam, created 3D printer “ink” from organic wood derivatives. As it dries, it warps into a design set by the scientists in advance.
In nature, plants and some animals can alter their own shapes or textures. Even after a tree is cut down, its wood can change shape as it dries. It shrinks unevenly and warps because of variations in fiber orientation within the wood.
Scientists in recent years have begun printing flat sheets that could form themselves into 3D shapes after a change in temperature, pH or moisture content. But these self-morphing sheets were made from synthetic materials such as gels. Kam and the other researchers wanted to go back to the roots of this concept, and do it with wood.
Layani, along with co-founders Prof Shlomo Magdassi and Prof Oded Shosayov, licensed the basic formulation, and tailored it to suit mass manufacturing processes.
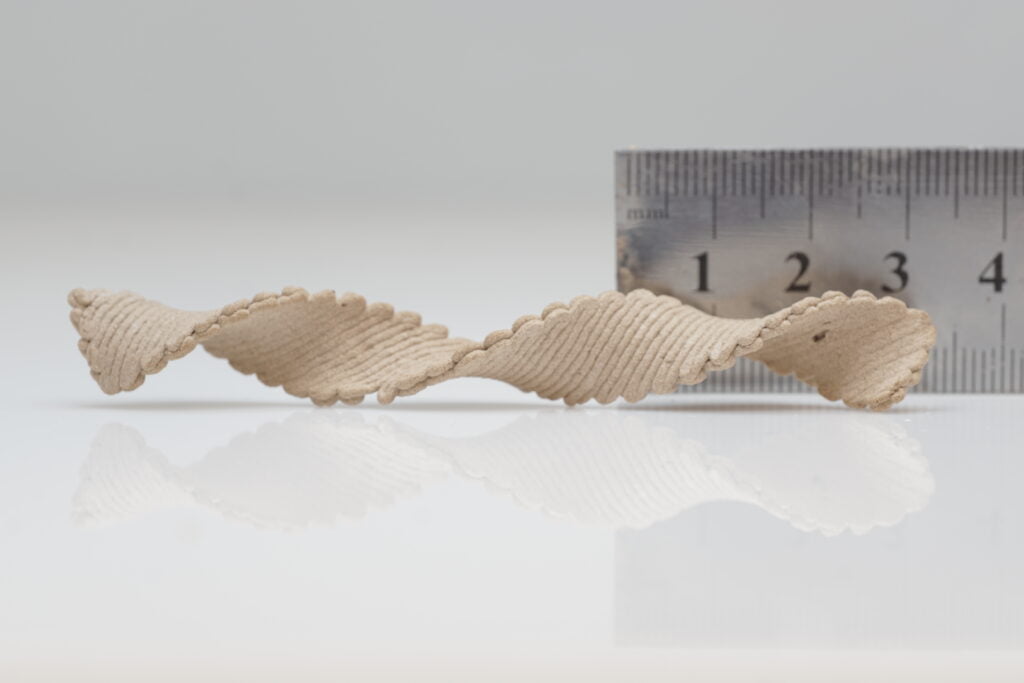
Eventually, Daika wants to expand into other products like consumer electronics and toys, but in the meantime it’s found a social benefit for its technology.
In Michigan, USA, Daika has partnered with Goodwill, the nonprofit that provides job training and opportunities. Around 20 per cent of its thrift-store donations are furniture, the vast majority which aren’t sold on. Daika uses the wood to make picture frames in scheme that provides jobs for the unemployed.
Layani says there are billions of tonnes of wood waste from agricultural, municipal and industrial sources – and the only solution currently is to burn it.
Sign up for our free weekly newsletter
Subscribe
But this option won’t be around for much longer. The EU is limiting subsidies for burning wood for fuel, and under its emissions trading system companies will be fined for exceeding set limits on pollutants.
And 12 states in the US, including California and New York, also have carbon pricing schemes that may limit companies’ ability to burn wood waste.
Wood is also becoming increasingly expensive. Prices fluctuate more than other products, typically because home repairs and remodeling are highly cyclical activities.
And it’s a scarce resource, with demand increasing faster than supply. As the world’s population grows, more people are moving into urban areas, and there is less land available for forestry.
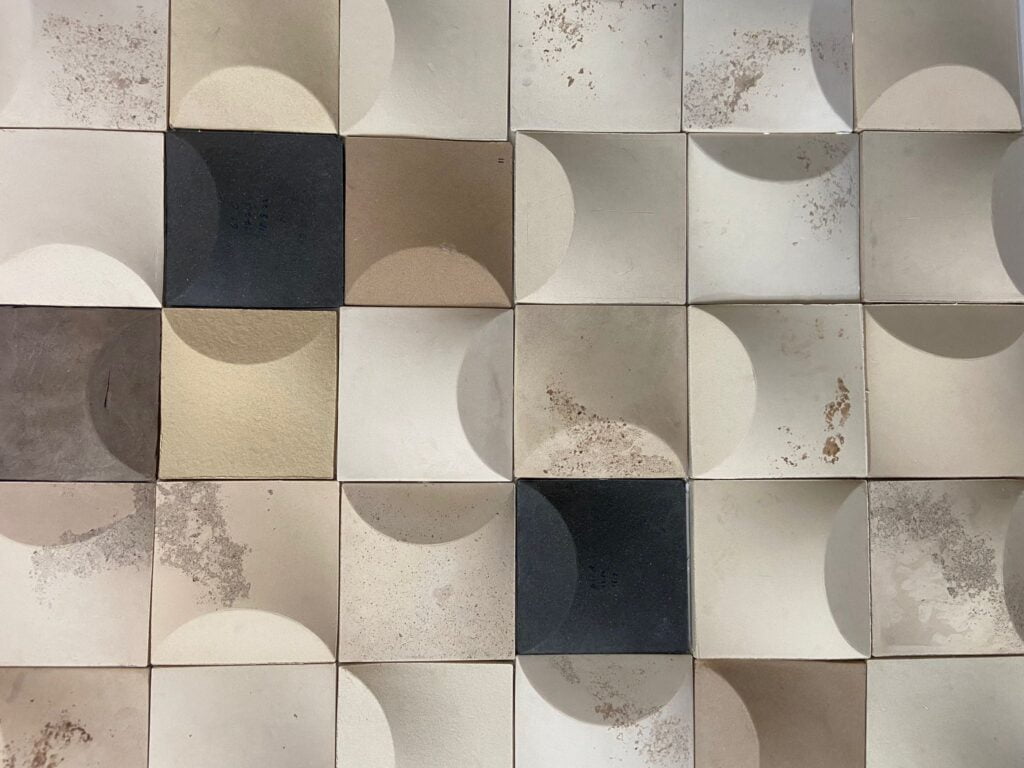
That’s why most companies use MDF, an engineered wood products that is usually bonded with formaldehyde, which is known to aggravate allergies, asthma, and cause other respiratory illnesses.
MDF is also not strong or durable like solid-wood furniture, stains easily, and is weakened quickly by heat, humidity, use and water exposure. It’s not water resistant, and can swell when exposed to it.
“If you look at all these problems, you don’t have a solution that is 100 per cent natural, cost competitive, and is applicable for mass manufacturing processes,” says Layani.
“And this is exactly what we’re here to offer to mass manufacturers. They don’t need to reinvent the wheel: they can use existing machinery and processes.”
Daika is mainly focused on saving industrial wood waste from sawmills. When these facilities chop down trees to make raw blocks of wood, millions of wood chips are created that go to waste.
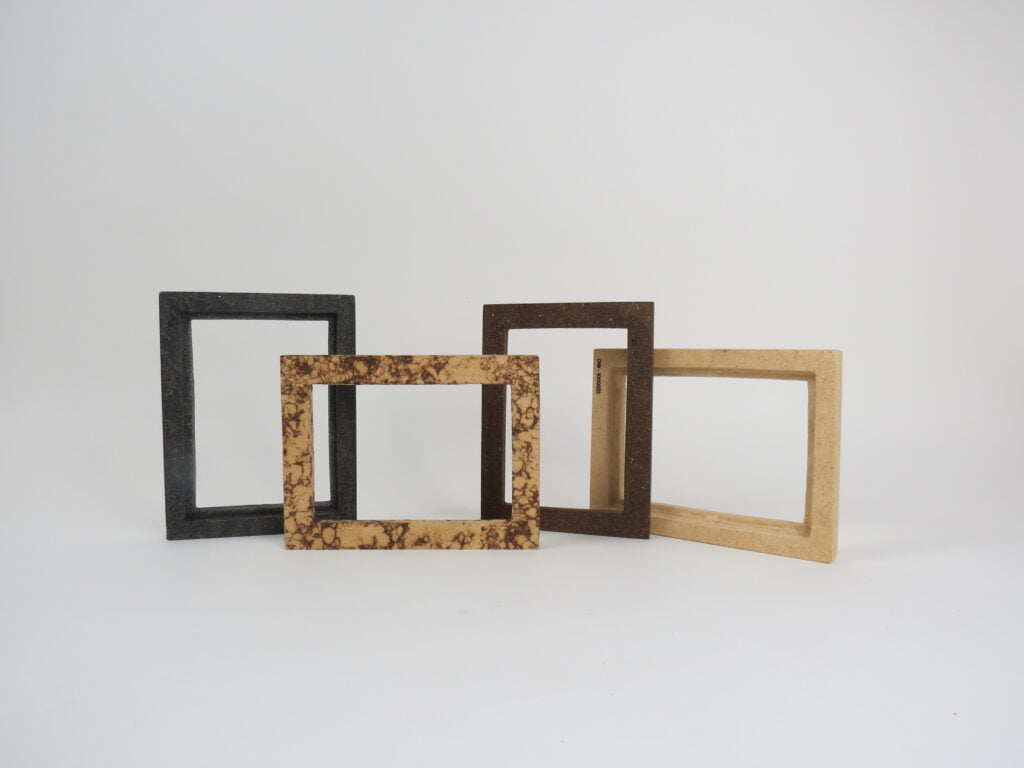
“There is no real solution to these huge amounts of wood waste,” says Layani. “Today, you’re drinking from a plastic bottle, and you know you can put it in a specific bin, and it has a solution to be upcycled and turned into a different product.”
Daika currently sources its wood chips from partnerships with sawmills in Sweden, Finland, and in Michigan, USA. There are tens of thousands of sawmills around the world, all producing vast quantities of wood chip.
“We’re here to tell them, ‘listen, instead of burning it, join forces with us and have a real circular solution.’”
The majority of companies trying to tackle wood waste are only able to combine plastic products with small amounts of wood waste. The other existing alternative is using other natural waste streams to create consumer products, like fungi and mycelium.
“But it’s a very slow and long-term process that requires complicated equipment to get the final product. And the end result is nowhere similar to what we do.”
“We’re not trying to completely replace plastic – it has its own benefits, such as water applications,” says Layani. “There’s room for both applications, but we’re offering another set of products that can be sustainable, can have an aesthetic appeal, and be completely upcycled.”
Related posts
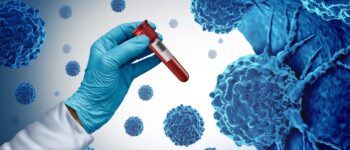
Editors’ & Readers’ Choice: 10 Favorite NoCamels Articles
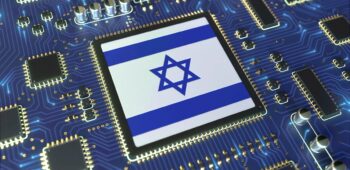
Forward Facing: What Does The Future Hold For Israeli High-Tech?
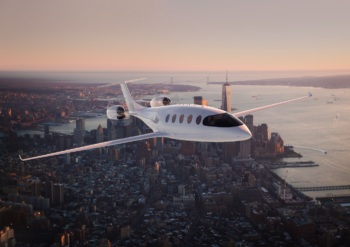
Impact Innovation: Israeli Startups That Could Shape Our Future
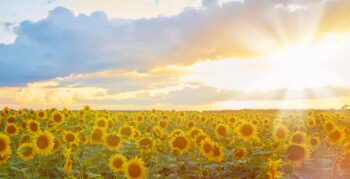
Facebook comments