A revolutionary solution for creating patient-customized devices has become instrumental in treatment of wounds sustained by people in the October 7 Hamas attack on southern Israel as well as IDF soldiers wounded in the subsequent war in Gaza.
Patient Specific Instruments (PSI) were initially introduced to Israeli hospitals seven years ago by the Netanya-based company Synergy 3DMed, but have become a reliable tool since the start of the war.
The technology involves using advanced 3D printing techniques to create PSIs and devices in point-of-care 3D printing labs, for procedures such as bone reconstruction and joint replacement. This allows for quick preoperative planning by surgeons using 3D visualization models as well as physical colorful segmented 3D models.
“Everything we are doing now we did before the war but now because [the technology] is available so fast, the physicians were able to use it very fast,” Michael Librus, CEO of Synergy 3DMed, tells NoCamels.
“Once you have all these materials and tools, you can think out of the box and you can produce a prosthesis and customized implants inside the hospital,” he says.
“You are able to do in a few hours now what the patient had to wait [weeks or months] for before to get something anatomically customized.”
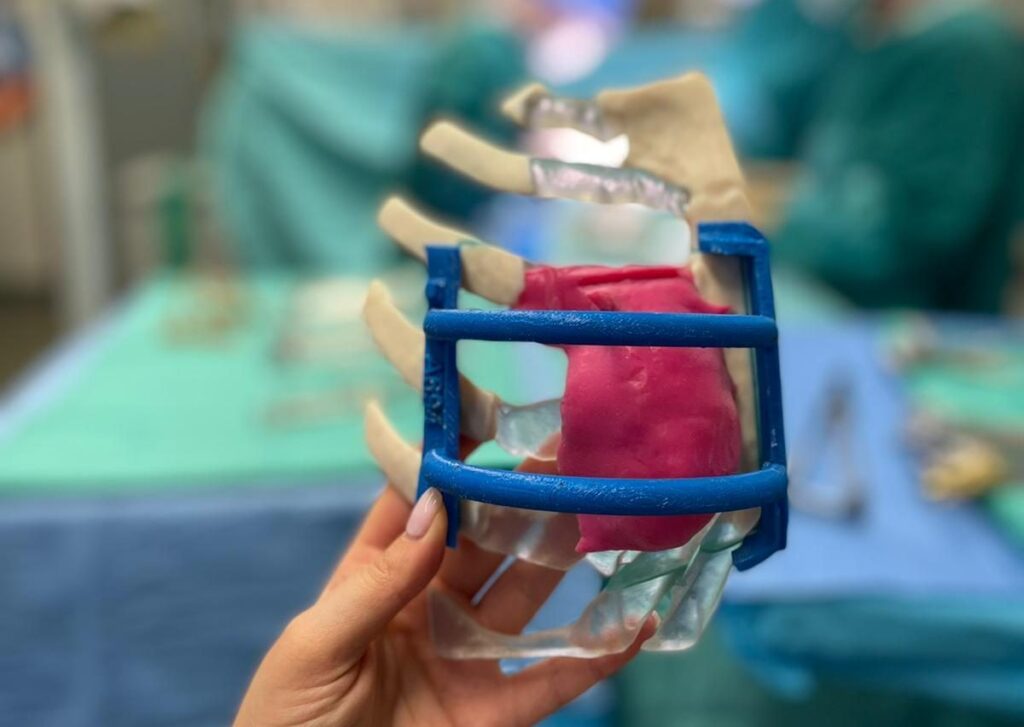
The printing tech is currently located at Ichilov Hospital in Tel Aviv and Hadassah University Hospital-Ein Kerem in Jerusalem, with a new lab being built at Schneider Children’s Medical Center in Petah Tikva.
Following a CT scan, Synergy 3DMed medical designers can create a 3D virtual segmentation model in consultation with surgeons, which they can manipulate on screen.
A physical 3D segmented model can then be printed, which the surgeons can manually manipulate – allowing for preoperative planning of what PSI is needed, and how to use and place it.
This allows them to go into an actual operation already knowing what they need to do rather than having to decide during the operation, which, notes LIbrus, allows for a safer and shorter operation time.
“The delivery time is incredibly fast and that’s the game changing ability to be on premises at the facility with the people and software to support [medical staff] inside the hospital,” he says.
“The physicians were able to go back to the lab, [see] exactly what they needed and then go back to the patient. And in a few hours they got the tools they needed—whether it was the segmentation or 3D virtual planning that they asked to see.”
Being able to treat patients quickly has been a significant factor in being able to reduce recovery time in hospital, allowing patients to go home or to a rehabilitation facility sooner, freeing up hospital beds for other patients.
This is crucial during this time in particular, when Israeli hospitals are receiving hundreds of wounded patients at once.
In addition, Librus says, quick treatment time has been shown to help a patient’s self-confidence as well as confidence in the medical team. This in turn has also been proven to help with recovery time.
Once a patient is shown the printed 3D model and is actually able to see and understand the procedure to be performed, they are more likely to cooperate in the rehabilitation process, he says.
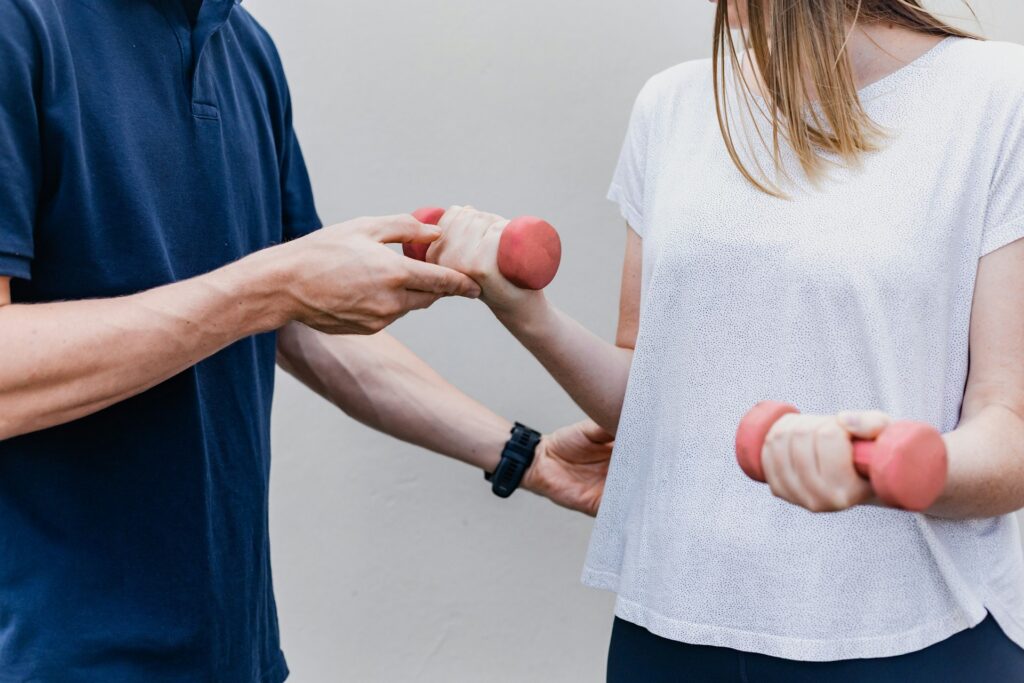
Librus, who studied industrial design in the USA and Italy, originally founded the company as a design studio using 3D printing methods to create prototypes for customers.
Seven years ago, they were asked by Stratasys, a leader of industrial 3D printing and additive manufacturing solutions, to take their design capabilities and production facilities into Israeli hospitals to use new biocompatible materials for surgical needs.
Librus credits the “entrepreneurial” surgeon Dr. Solomon Dadia, then deputy director of orthopedic oncology at Ichilov and today the hospital’s head of the surgical innovation and 3D printing unit, as being pivotal in helping introduce the pioneering technology into Israeli medical facilities.
Sign up for our free weekly newsletter
SubscribeRecently, an Israeli TV news segment highlighted the 3D printing of a PSI device for an IDF military dog who had had part of his skull shattered in a military operation in Gaza.
A CT of the brave canine’s head provided the surgeons with a look at the shape of the missing piece of skull. Medical planners of Synergy 3DMed were then able to recreate the segment and the surgeon fit it—almost like a missing puzzle piece—into the skull of the dog, who fully recovered after the operation.
The same process was used for a soldier who sustained similar injuries in Gaza: Synergy 3DMed medical designers were able to provide surgeons with an exact printed PSI which was fitted to safely close up the skull.
The news report showed the soldier, post-operation, visiting neurosurgeon Prof. Jonathan Roth, head of the neuroendoscopic unit at Ichilov, and smiling as he incredulously held the printed 3D model that had assisted the physician in the operation.
“Each procedure is a unique opportunity to help someone,” says Librus.
“Sometimes it’s a dancer who you help reconstruct her broken leg so she can dance again, and sometimes it’s a dog to support him to go back to living. We owe them this as human beings to give them back their lives.
“Each story is mind blowing because you know this patient will not need any revisions later and they will be back contributing to the country, and will have back their quality of life.”
The procedure has been used in over 2,000 cases in 25 hospitals – mainly in Israel but also in England and Spain. It was used in 16 different surgical disciplines, including in oncological surgical treatments reducing bone loss, as well as for repair of congenital malformations.
“Everybody gets real benefit from having access to this material,” says Librus.
“The physician can be very creative, and create their new method of work or solution; they have this flexibility of materials.”
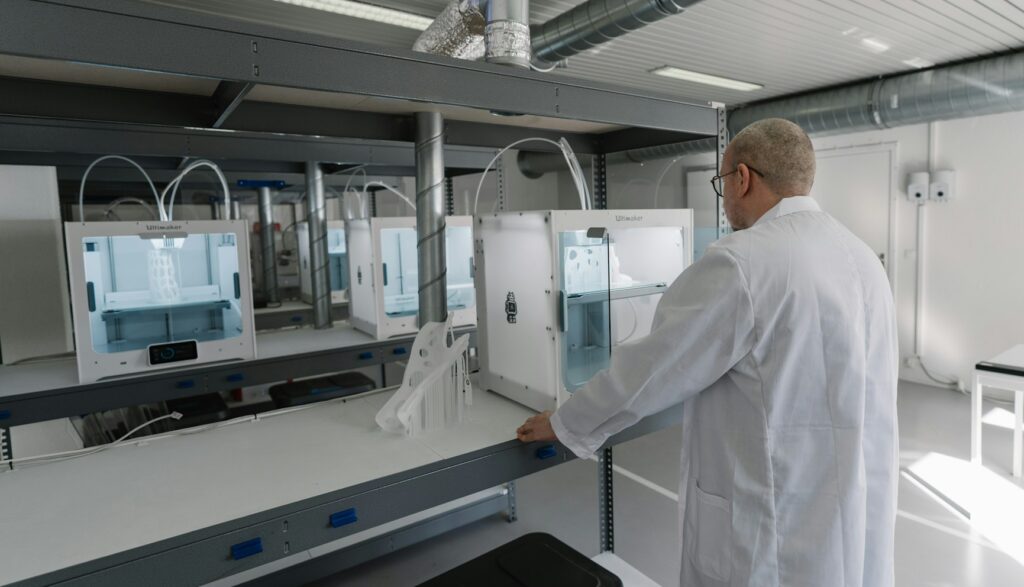
Part of the company’s strategy has been to create an academic program at the Holon Institute of Technology for medical designers who will be needed as this technology expands, Librus explains.
“You need to think differently to create innovation to be very multidisciplinary, to connect together chemistry, physics, electronics and to create a solution that mixes a lot of knowledge,” he says.
“We are working to create new students who are very multidisciplinary.”
Medical technology companies such as the global leader Medtronic are realizing this is the future of the industry, says Librus, and a few other companies worldwide have begun working with similar technology.
As for Synergy 3DMed, its next mission is to raise $8 million to move into the United States and Europe.
“Now we need to duplicate this to the rest of the world. If we are not spreading this to the rest of the world we are not contributing to humanity,” Librus says.
He notes that while Israel is a “great place” for R&D and to create innovation, to scale up, the technology must be introduced into the rest of the world.
“This is what we will be doing in the next few years. We’ll finish this war, the economic situation will be better and then we will continue with the journey we started seven years ago.”
Related posts
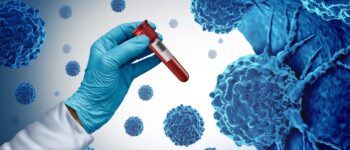
Editors’ & Readers’ Choice: 10 Favorite NoCamels Articles
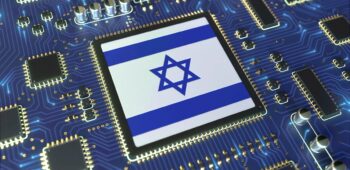
Forward Facing: What Does The Future Hold For Israeli High-Tech?
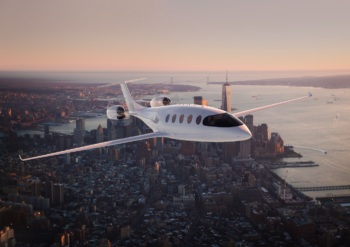
Impact Innovation: Israeli Startups That Could Shape Our Future
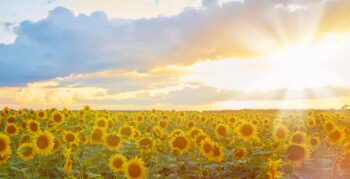
Facebook comments