Israeli startup develops a fully compostable alternative
An Israeli startup has developed a breakthrough process that literally turns food and clothes packaging into garden compost.
It breaks down into tiny parts that are eaten by bacteria and turned into regular soil. Compare that with ordinary plastic that takes 500 years to biodegrade, and even then will remain in our environment as microscopic particles forever.
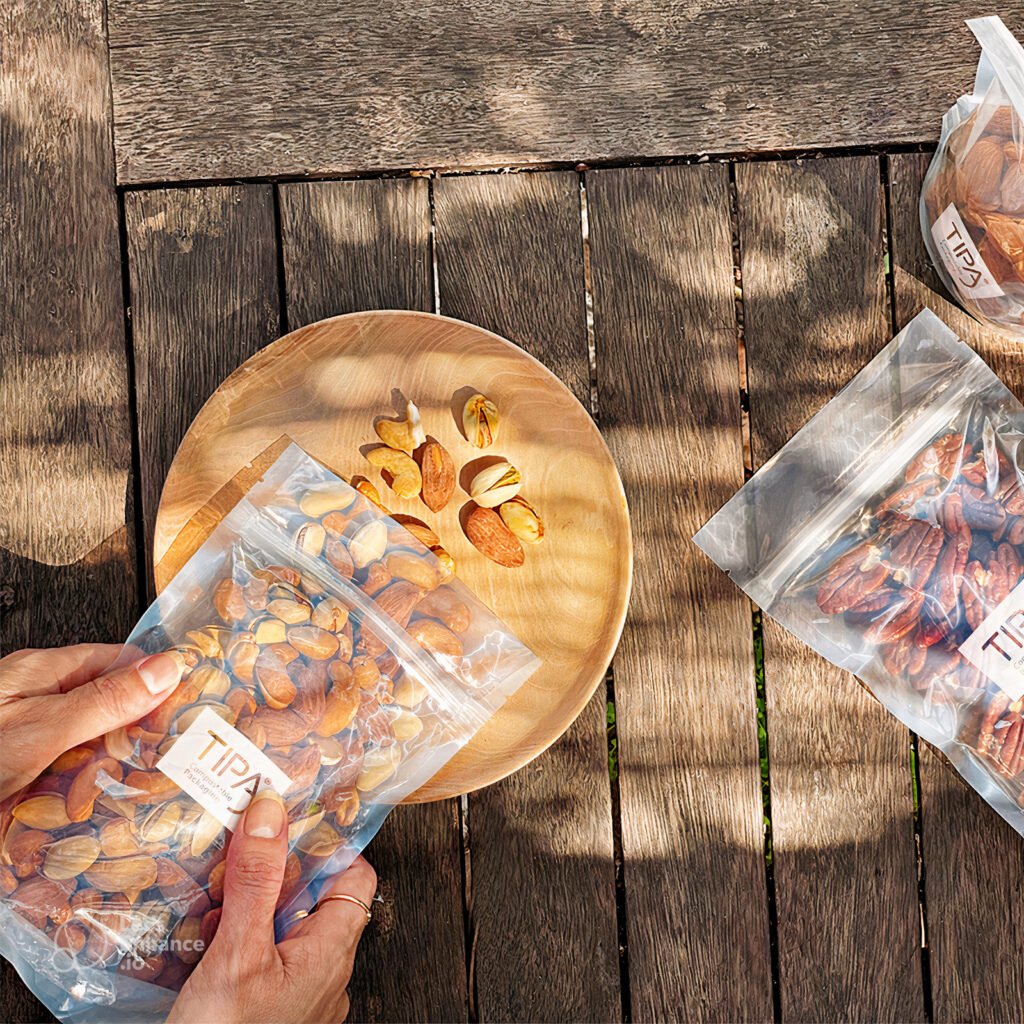
“The idea of Tipa was to emulate nature,” says Daphna Nissenbaum, the company’s CEO and Co-founder.
“Nature also packs its products, like bananas, apples, and oranges, but with a compostable material. Our plastics will disintegrate and biodegrade exactly like any other organic material, and turn into solid fertilizer.”
“Plastic is piling up, even if we don’t see it. Every piece of plastic that was ever manufactured is still someplace around us. And although we think we treat plastic, it stays here.”
There are other compostable plastics out there, but many of them have a greasy feel or a milky color.
Not only that, but a recent two-year study found that 60 per cent of the plastics certified as home compostable in the UK did not fully disintegrate in home compost bins. The 1,648 participants who used the compost in their flower and vegetable gardens were inadvertently adding plastic to the soil.
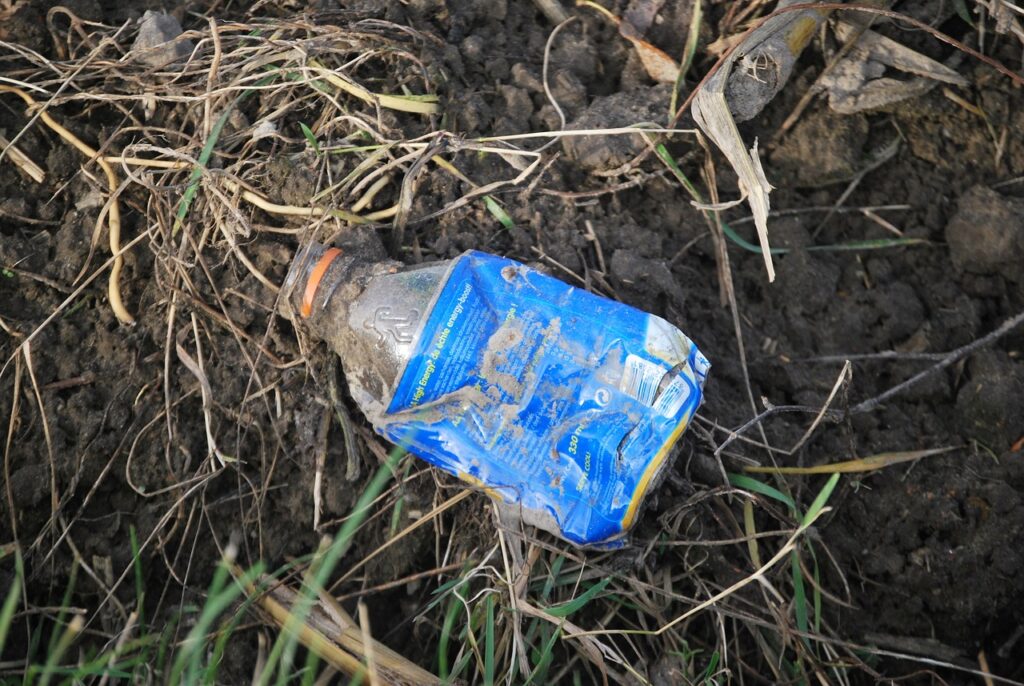
Tipa’s plastics have the same elasticity, durability, and look and feel as conventional ones. The only difference is that they use a handful of additives – which the company wouldn’t share with us – to ensure that they will be fully compostable, under the right conditions.
Composting is the natural process of recycling organic matter, like leaves and food scraps, into a valuable fertilizer. If the pile is layered correctly in a home compost bin, with the right combination of organic matter, air, and water, it will heat up within three days to the ideal temperature of 141°F to 155°F, and macro- and micro-organisms will begin to break it down.
Tipa specifically focuses on creating fully compostable flexible packaging – any package which has a shape that can readily be changed when filled or during use – like films and laminates.
“The reason we decided to focus on flexible packaging is because it cannot be recycled, period,” Nissenbaum tells NoCamels. “The recycling rate is around four per cent globally. It’s also a billion dollar industry. We want to focus where there’s a real need.”
Tipa doesn’t manufacturing the raw materials. It orders them from suppliers according to specific criteria and properties to ensure they’re compostable either at home or industrially
At its lab in Hod HaSharon, central Israel, it constantly tests new raw materials (once they’re made into plastic film and laminate samples), including their elasticity, how much weight they can hold, and how resistant they are to water and oxygen. It also tests the sample laminates and films in-house, putting shreds of them into chambers to monitor their compostability.
Sign up for our free weekly newsletter
Subscribe
Guy Zylberstein, Process Engineering Manager at Tipa, says: “Everyone can buy the same grade of the same raw material. But they will never be able to put the right percentages of the raw materials themselves to create compostable films that look, act, and feel like regular plastics.”
Compostable packaging will help reduce landfill, but food, paper, yard waste, and wood still account for 51 per cent of the trash that is dumped annually.
Despite this, only 27 per cent of Americans have access to some form of composting service. The United States has limited funding for composting pick-up services (only three per cent of Americans enjoy municipally-run curbside access), and few facilities that consumers can send their compost to.

Home composting is not viable for everyone, either. It requires a lot of work, with people needing to move it around a few times a week to ensure proper air circulation, and it takes time until all the food waste is decomposed into useful compost. Plus, lots of space is required, compost gives off an unpleasant smell, and it can attract animals like rats and bugs.
But Nissenbaum truly believes that Tipa will help the world adopt composting, even if not all countries are there right now.
“The name of the company, Tipa, means ‘a drop’. I think every drop makes a change,” she says. “So by purchasing compostable materials, we encourage the compostable industry to grow, and encourage the compostors to accept more compostable packaging, and encourage the legislators to support the growth of solutions.
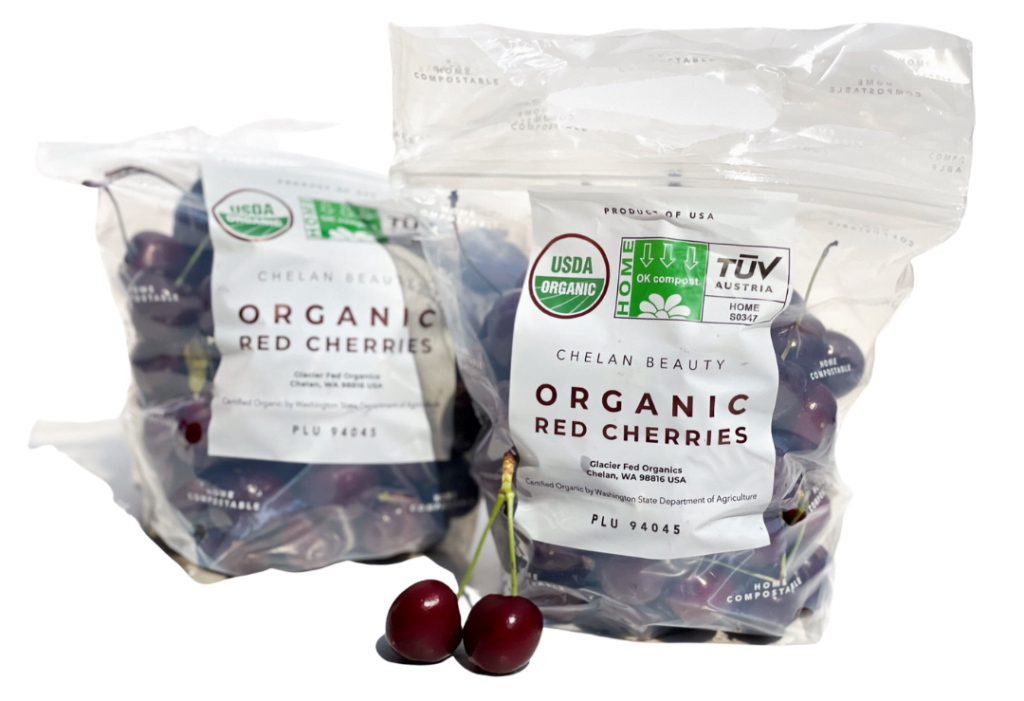
“And we all have to work on it. We do our part, governments need to do their part, brands need to do their part. All together there’s a ground to make the needed change in how we consume plastic.”
Tipa works with a number packaging manufacturers, like Altapac, a packaging and pouch converter in Ohio, USA, because its secret process can be seamlessly integrated into their machinery.
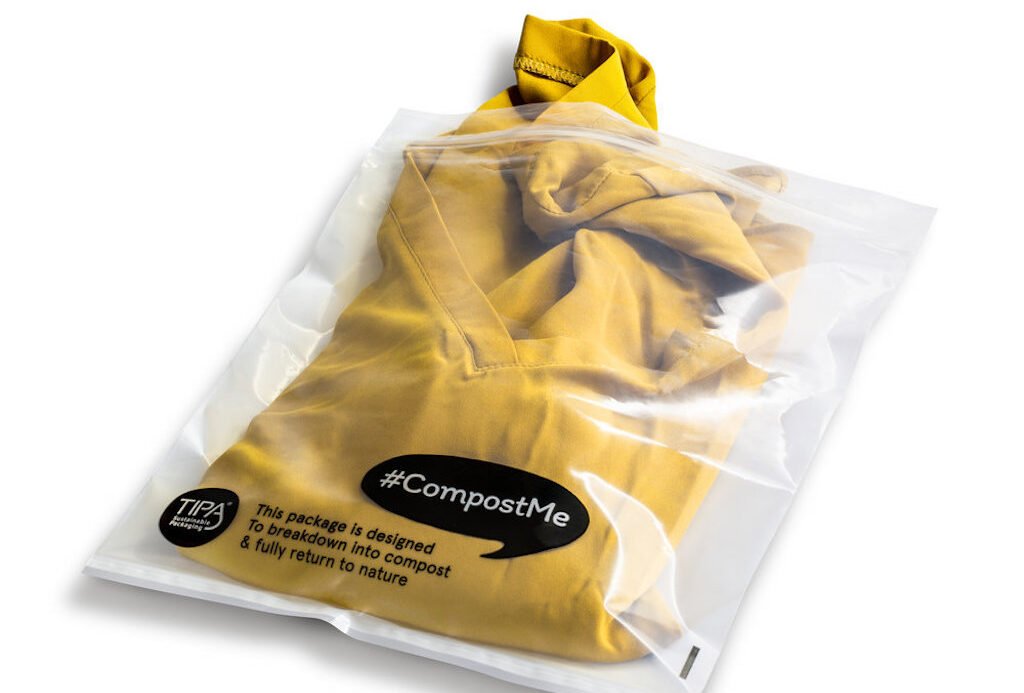
“Because we know how to work on their machines, we bring the knowledge, and this way we turn them to be our partners instead of our competitors,” says Nissenbaum “We don’t want to compete with them. We want them to be part of our supply chain.”
Tipa also sells its plastic packaging to a number of brands, and has its products manufactured local to them. It supplies its packaging to Jane’s Dough (a frozen pizza company) and Sunrays Grapes, eye drops supplier MTHK, and clothing companies including Pangaia, British menswear L’estrange, and cycling clothing producer Isadore.
Tipa’s packaging needs to be composted, but it will biodegrade if it’s thrown into a landfill, under certain conditions. Nissenbaum says that even throwing away her packaging is better than throwing away ordinary plastic packaging, which will never fully disintegrate.
“We don’t want the package to release methane, so that’s why we want it to be in the compost system, like organic waste, and like any of the cucumbers and tomatoes that we eat,” she says.
Related posts
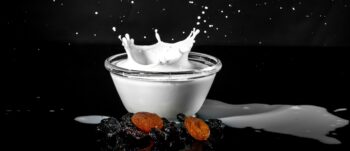
Resilient And Nutritious New Plant-Based Milk Aims To Make A Splash
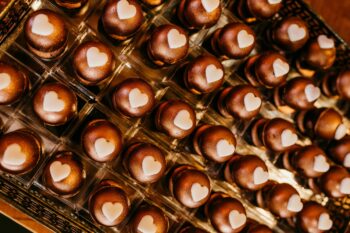
Chocolate From Cultivated Cocoa Comes Without Environmental Toll
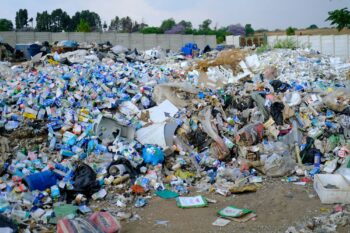
Plastic Fantastic: Startup Takes PVC Back To Its Crude Oil Roots
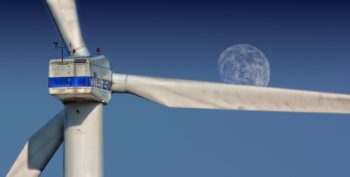
Facebook comments