Startup sprays color onto yarn, saving millions of wasted gallons
Fashion is one of the world’s worst polluting industries. Dyeing yarn for clothing alone accounts for over a fifth of global water pollution.
But an Israeli company has developed the first dyeing system in the world that is completely water-free.
It uses a method that’s closer to printing than traditional dyeing. Twine Solutions, based in Petach Tikva, central Israel, precision-sprays the yarn with a dye specially designed to penetrate every fiber, rather than using conventional methods that need huge volumes of water and chemicals.
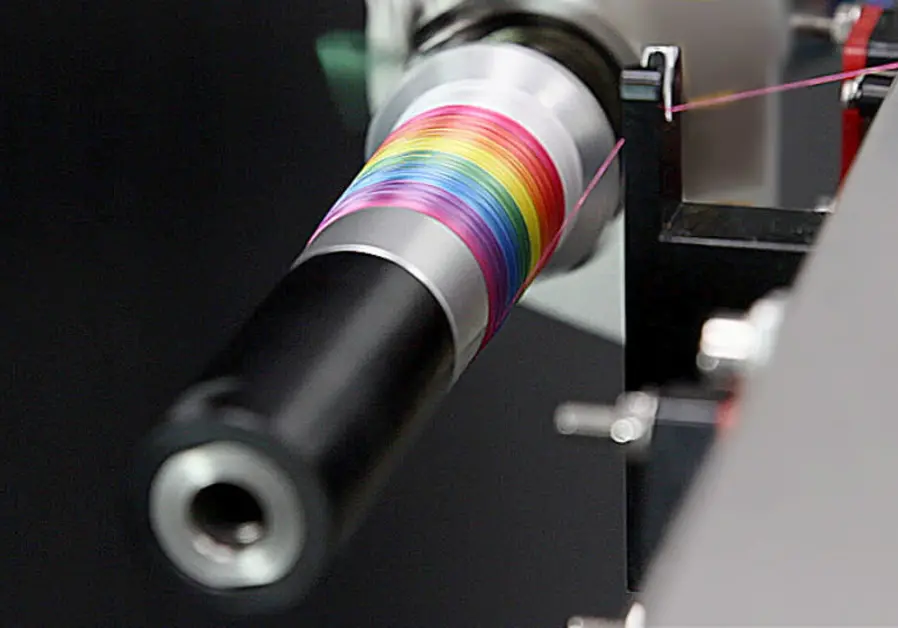
Its machine produces the samples of yarn that clothes designers need for color checks in a matter of minutes – a quick and effective alternative to having a dye house crank up the whole resource-heavy process for a small run.
Twine Solutions hopes, eventually, to scale up its machinery to handle bulk orders. But it says the textile industry is very traditional, and many of its processes – including yarn dyeing – haven’t changed in decades.
Suppliers of dyed yarn say customers will, it says, resist any move that could raise the cost of a finished garment by as little as a penny.
“Our machine is a cost-effective solution because companies can prototype and sample much faster than their competition,” says Adi Mandel, Senior Marketing Manager at Twine, tells NoCamels.
“They can be more agile, they can adjust much faster, and they can gain customers they might have missed because they normally would not have had the right color.
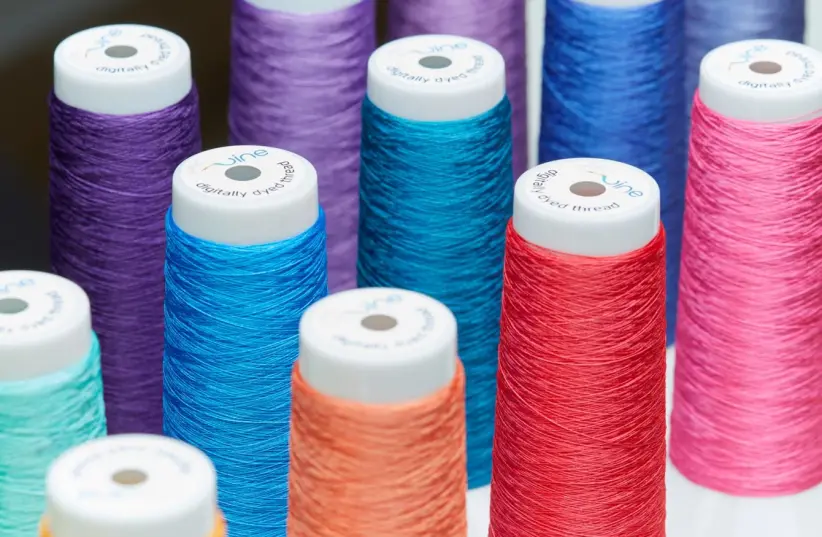
“When a manufacturer needs to produce a sample or prototype really quickly, it helps the brand to be the first, and it helps the brands to put their product in the stores faster, because they saved a lot of time and money during this process.”
There’s a remarkable amount of back and forth before a newly-designed garment actually goes into production. Designers create swatches – a piece of fabric with their chosen design and color – and send it to their manufacturer.
They in turn send the swatch to a dye house, to produce their three best matches using traditional water and chemical methods. If the designer and manufacturer are happy, that’s fine. If not, the dye house will have to try again.
The swatches then travel around the world for approval by sales teams in different countries and regions, which means another batch of samples needs to be prepared.
Twine’s machine can dye nearly 6,000 feet (1,800 meters) of polyester yarn per hour. All the user needs to do is load raw or white thread, and choose the desired color and length on its touch screen, and it does the rest.
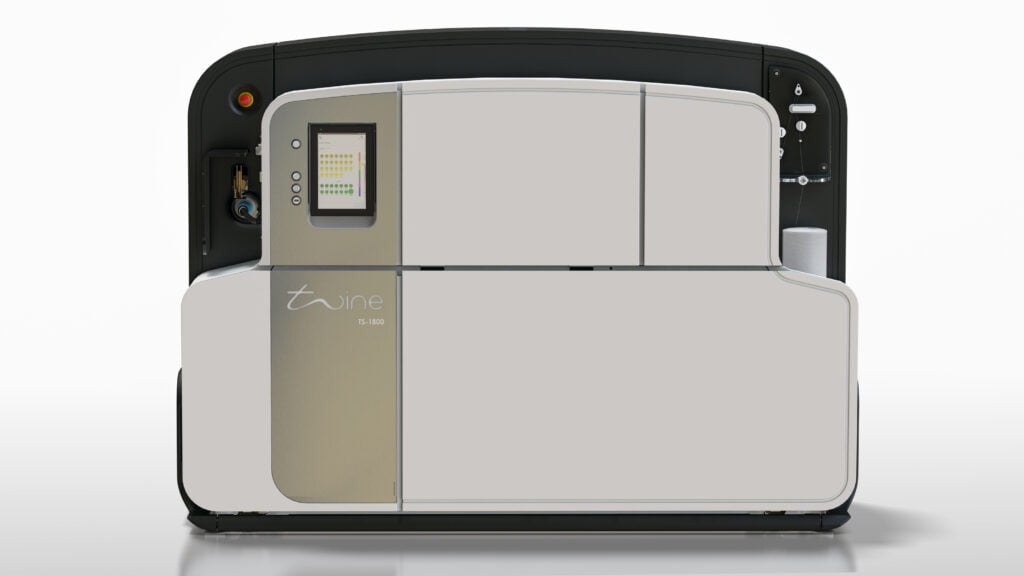
“You’re saving so much time and so much waste, so much hassle and air emissions because of these planes going back and forth. The process is so much more simplified,” says Mandel.
Sign up for our free weekly newsletter
Subscribe“Ordering more yarn and thread, testing, understanding it’s not the right one, buying again – all of this creates huge piles of waste within the industry.
“The best thing that can be done is the manufacturer or the brand can send them a spool of thread that was dyed with Twine, and they can match it,” she says. “Brands can prevent a lot of waste and waste water being generated.”
The waste water produced by the dyeing process is used to irrigate fields in China, Thailand, Bangladesh, Indonesia and other countries that dominate the dyeing market.
It pollutes rivers and oceans, and is incredibly dangerous for people. Last January, six workers in an Indian dyeing mill were killed, and over 20 were hospitalized after inhaling toxic gas caused by an illegal dump of waste chemicals.

Twine is the world’s first digital and water-free thread dyeing system, though in recent years some competition has begun to emerge.
Coloreel, a Swedish company, has developed a device that connects to embroidery machines and digitizes the dyeing process as well – but producers can only use the company’s dedicated thread.
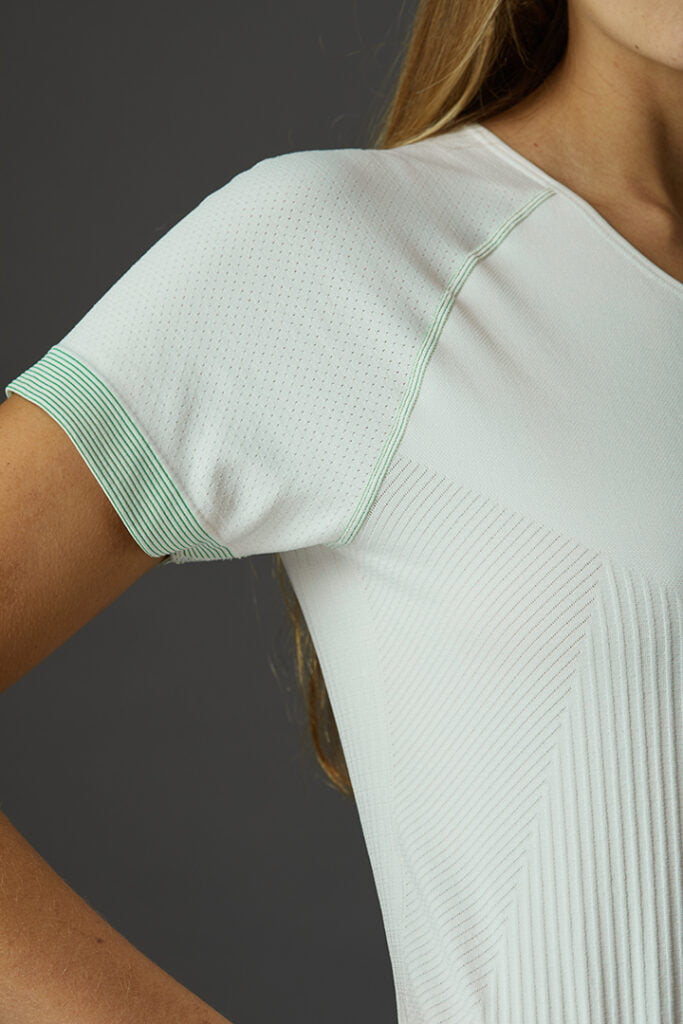
Alchemie Technology, in England, also uses a digital dyeing process for polyester fabrics, but is not completely water-free.
Twine Solutions was founded in 2015, and debuted its machine, the TS-1800, at a trade show in Barcelona in 2019.
Since then, it has been implemented in development centers, R&D centers, and near production lines around the world, in Asia, Europe, and the US.
Israeli textile firm Delta Galil used the Twine machine to produce a one-off collection of Nike socks. “They created a gradient effect, so each pair was unique. The label mentioned how unique and sustainable the sock is,” says Mandel.
The company is also working with Coats, the world’s leading industrial thread manufacturer, to create a specific color of yarn without a sample or swatch.
It’s a collaboration that could be the first step towards scaling up its machinery to handle bulk rather than sample orders.
Related posts
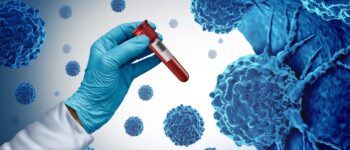
Editors’ & Readers’ Choice: 10 Favorite NoCamels Articles
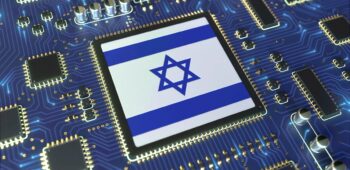
Forward Facing: What Does The Future Hold For Israeli High-Tech?
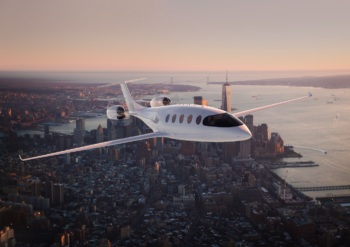
Impact Innovation: Israeli Startups That Could Shape Our Future
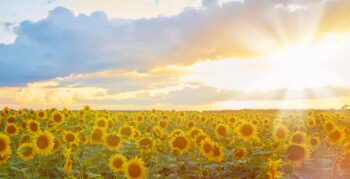
Facebook comments