Israel-based startup REE Automotive, the auto tech firm that produces flat chassis designs for electric and autonomous vehicles, has announced that it is set to build a UK manufacturing center that will cover 130,000 square feet. It will also include a commercial assembly line operated by autonomous robots to supply customers in Europe.
REE will partner with industry leaders like Rockwell Automation and Expert Technologies for robotics and automated assembly, with the first assembly line expected to become operational in the second half of the year, the company said in a statement.
Founded in 2011 and emerging from stealth mode six years later, REE Automotive developed a technology that enables a completely flat and modular chassis for electric and autonomous vehicles that allows multiple body configurations on a single platform, reducing space and weight and increasing efficiency. The company developed an entirely flat and modular platform that incorporates REEcorner technology. REEcorner tech integrates the motor, steering, suspension, drivetrain, sensing, brakes, thermal systems, and electronics are all integrated into the vehicle’s wheels.
“REE is based in Israel. We’ve got the research and development based in Israel. The software is based in Israel. We’ve got an engineering team now which I’m leading in the UK, which is taking that automotive experience that we’re bringing as our knowledge so that we can industrialize our products ” Peter Dow, REE’s Vice President of Engineering, tells NoCamels on a video call during a visit to REE’s Tel Aviv-based offices, “So how do we make it in the thousands? How do we make it so it’s durable, reliable, safe, meets all the regulations? That’s the experience that the UK team is bringing into it, which is kind of complimentary for the Israeli team.”
It’s a joint development, he explains, noting that the two teams are “intermingled.”
“We’re based in Coventry in the UK and we have an engineering development team that will do a lot of the testing development in the UK because they have very dedicated facilities that help us with that in terms of test tracks.”
The establishment of REE’s Coventry center is a “pivotal moment” in the commercialization of REE’s innovative REEcorner technology and EV platforms, according to the company’s statement. The center will focus on the P7 EV
REEs Coventry center will have an initial focus on the P7 EV platform for commercial electric vehicles such as walk-in delivery vans, buses, and recreational vehicles. Prototype on-track testing of the P7 platform has already begun this year, the company said.
The center will have an expected capacity of 10,000 vehicle sets (40,000 REEcorners).
The robotic element
The company intends to implement a cloud-based robotic assembly line at the center which will be overseen by a staff of about seven human employees.
Sign up for our free weekly newsletter
Subscribe“The robotic line allows us to build a REEcorner in less than a minute, one by one. I mean, seriously one by one. And with very little intervention from human operators. Then we can build a full line in six to nine months, wherever we need to be ready for manufacturing. There is not much knowledge that you need to teach the operators. Its all automatic, just get the gear and it’s ready,” Ohad Stauber, VP of R&D, tells NoCamels.
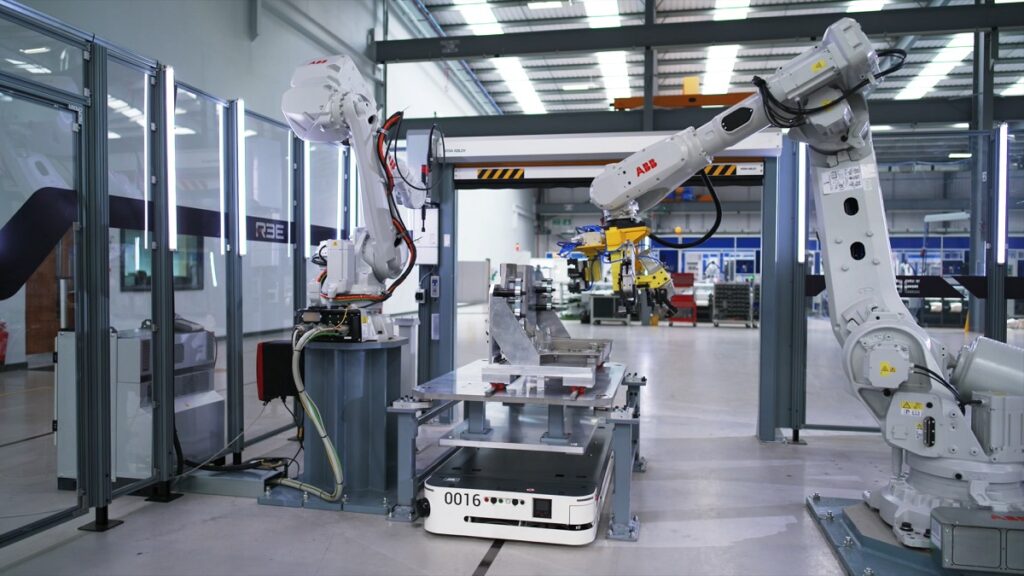
“The robotic control has been done in partnership with a couple of manufacturing, firms that develop manufacturing lines and development robot technology. And so it’s something that is our blueprint, it’s something that our manufacturing team has put together, which has been very much done in collaboration during the engineering phase. So we’ve engineered to manufacture as well. These are industry standard robots that have been tuned and bespoke for us,” adds Dow.
According to Dow, one of the purposes of an all-robotic assembly line is the ability to duplicate the process in different countries and areas for customers. This is where the cloud interface comes in.
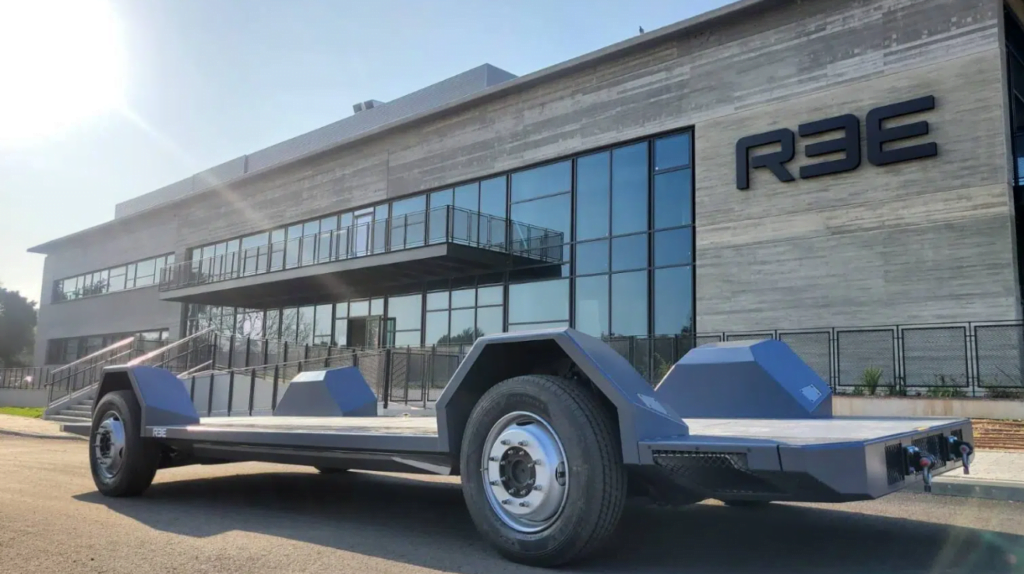
“So what we need is something we can copy and paste, really easily and quickly for four different applications. So we started in Coventry — it’s what we call our launch factory — we’ll do it there first and we’ll copy that and paste that into [the city of] Austin in Texas, where we can serve the US market. And we can copy and paste that throughout the world whether it’s Japan, Europe, Israel. We can decide where we want to do it,” he says, “And making it robotic, particularly with a cloud interface means that all of that knowledge that gets generated in the launch factory, the first time — how the robots operate, how to assemble the corner, sits in the cloud. And then once we copy that, and paste that into new territory, we just pull it down from the cloud in increments. The setup is very quick and efficient. So it’s all about duplication quickly and actually being able to service our customers closer to them.”
Last summer, REE announced plans for a US-based headquarters in Austin, Texas, expected to launch in the second half of 2022. REE has its headquarters in Tel Aviv, Israel is also starting to test the waters in the US and Germany. The Austin integration center is expected to double its global capacity to 20,000 vehicle sets in 2023.
“This is an important milestone on our path to commercial production next year. The automated and connected capabilities at our Coventry site are a great foundation for our global operations, as they will enable us to continuously fine-tune our assembly procedures and rapidly deploy them to other sites,” said Josh Tech, REE’s chief operating officer, in the statement. “Our cloud-based robotic manufacturing system will be the digital backbone for our assembly lines and give us the local capability to manage our customer-specific manufacturing operations, while also allowing us to quickly share and scale best practices internationally across all plants.”
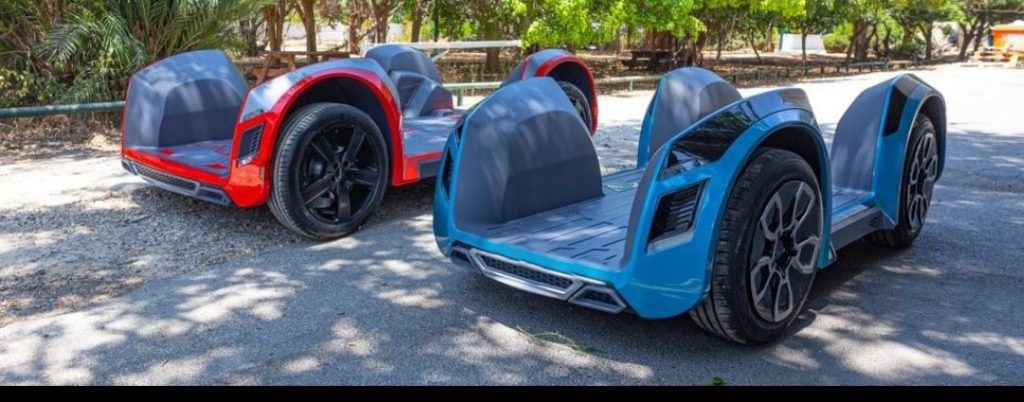
Earlier this year, REE announced it would commence trials of its all-electric P7 modular platform designed for commercial delivery vehicles and walk-in vans. The platform, targeted to a US-based delivery van platform was designed based on function and operational specifications from one of the world’s largest delivery companies, according to the announcement. Fully flat from end-to-end, the P7 offers greater interior space and volumetric efficiency for vehicles. The platform supports up to 8,800lbs and packs up to 35 percent more packages than comparable commercial vehicles. It can comfortably carry up to 30 passengers, making it optimal for delivery and logistic fleet owners, transit authorities, school buses, and mobility operators. REEcorner and X-by-Wire technology enable each wheel to move independently, the company said.
In February 2021, REE launched its first Engineering Center of Excellence at MIRA Technology Park in the UK to spearhead REEcorner and EV platform engineering design, validation, verification, and testing, as well as a pathway to production.
Related posts
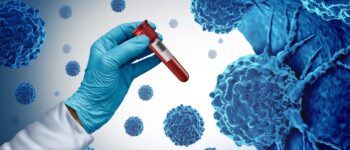
Editors’ & Readers’ Choice: 10 Favorite NoCamels Articles
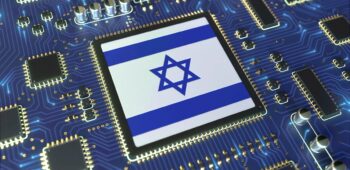
Forward Facing: What Does The Future Hold For Israeli High-Tech?
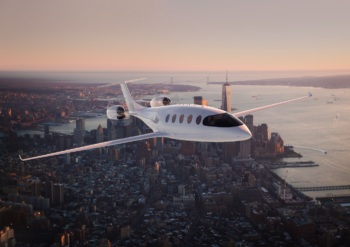
Impact Innovation: Israeli Startups That Could Shape Our Future
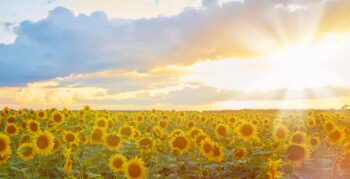
Facebook comments