German automotive giant Daimler AG announced on Tuesday that it was testing a waste conversion solution developed by Israeli company UBQ Materials for the production of “clean” automobile parts.
Daimler is embarking on a trial and development partnership with UBQ which will look at incorporating UBQ’s tech into the production of a range of Daimler automobile parts. The Israeli company developed an innovative, patented process to convert unsorted household waste (think chicken bones, hamburger leftovers, and yogurt containers) into a sustainable, fully recyclable thermoplastic substitute.
Following a number of trials, Daimler and UBQ will decide whether to pursue a go-to-market strategy, but both companies indicated that initial results have proven positive.
SEE ALSO: Bye Bye, Trash: Israeli Startup Pilots Breakthrough Waste Conversion Solution In US
Daimler will become the first automotive company to partner with UBQ, founded in 2012 by Rabbi Yehuda Pearl, a founder of the globally recognized hummus brand Sabra, and Jack “Tato” Bigio, an entrepreneur and leader in the renewable energy sector who also serves as CEO. The team emerged from stealth mode in late 2018.
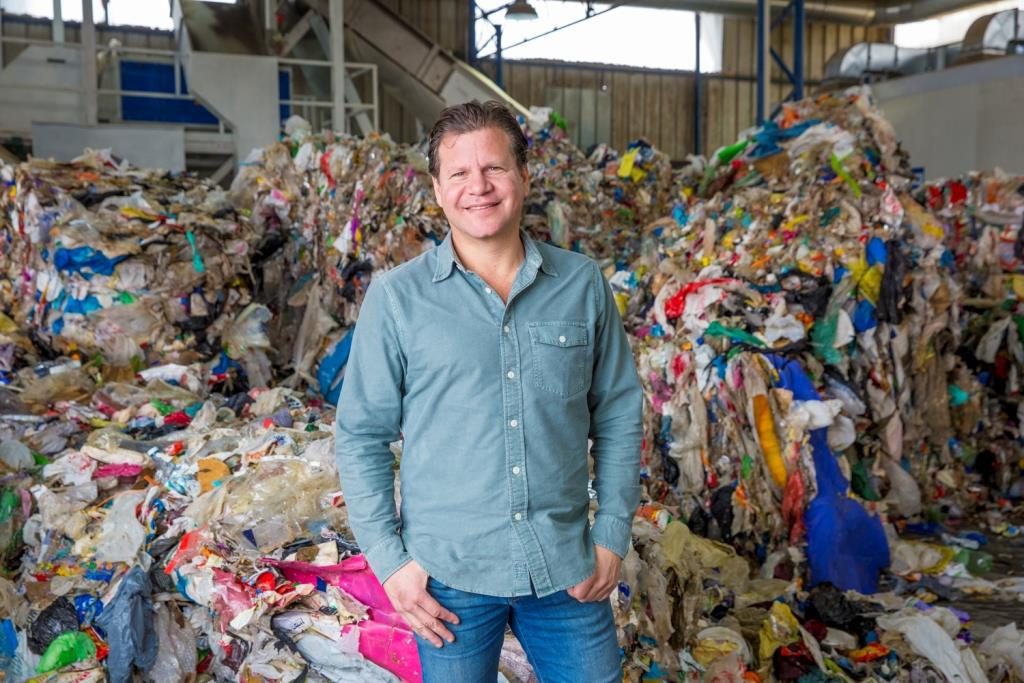
Bigio tells NoCamels in an email exchange that the auto parts in question will include injection molding parts and non-structural components such as door coverings, glove compartments, and connection boxes.
He adds that specific details on the results from the trial are currently under wraps but that they “are very promising.”
The partnership with Daimler was made through Plug and Play’s Startup Autobahn, an innovation platform that connects emerging technologies to pilot opportunities with multinational corporations. Daimler is also set to promote the use of UBQ materials with partnering logistics manufacturers to support the offsetting of carbon footprints across the Daimler supply chain, according to a company statement.
“UBQ is a conduit for the next generation of sustainable products,” said Bigio in a press statement. “We could not think of a more fitting partner than Daimler, which has long been a global leader in technical innovation and quality engineering and shares our commitment to the health of the environment.”
UBQ currently also has running partnerships with Arcos Dorados (or Golden Arches), the largest independent McDonald’s franchisee in the world and the company that operates the brand in Latin America and the Caribbean, and with the Central Virginia Waste Management Authority (CVWMA).
Sign up for our free weekly newsletter
SubscribeIn Latin America, the McDonald’s franchisee plans to replace some of the materials in McDonald’s restaurants with similar, more sustainable ones made using UBQ technology. In Virginia, UBQ delivered some 2,000 recycling bins made with UBQ Materials’ converted waste material.
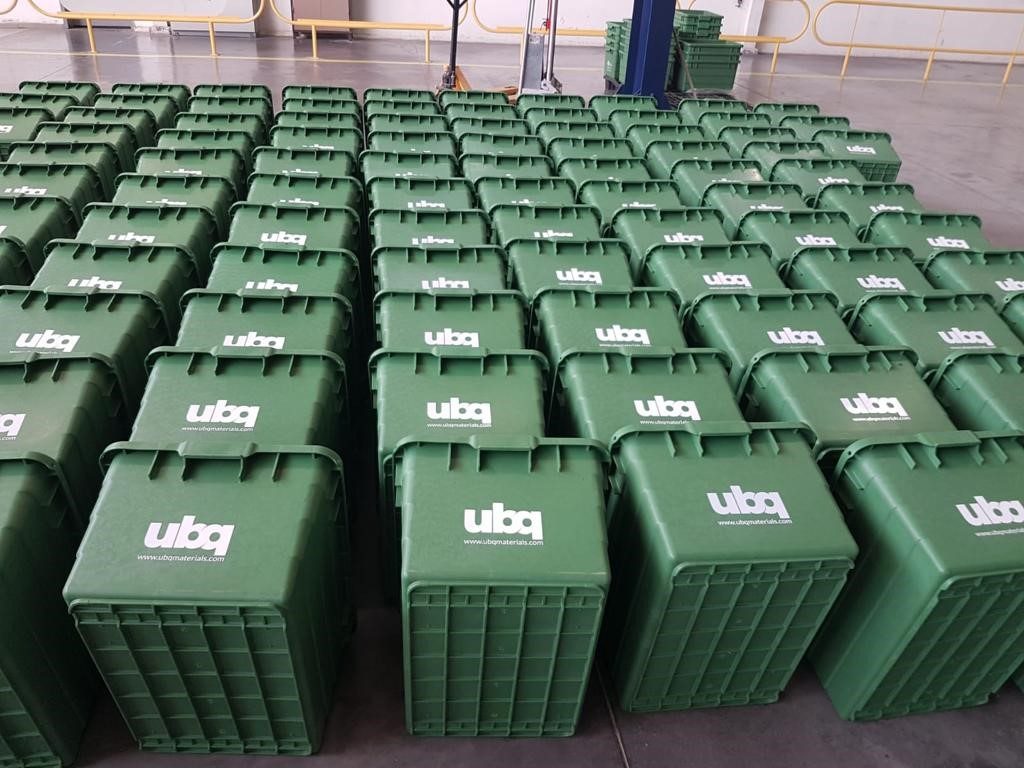
UBQ runs a plant in Kibbutz Tze’elim in southern Israel where some 7,000 tons of garbage is converted per year. The company plans to open a full-scale facility in the United States later this year and hopes to add additional locations in Europe, and Asia.
As a raw material, UBQ says that its products can be used in thousands of applications including shopping carts, pipes, trash cans, and automotive parts.
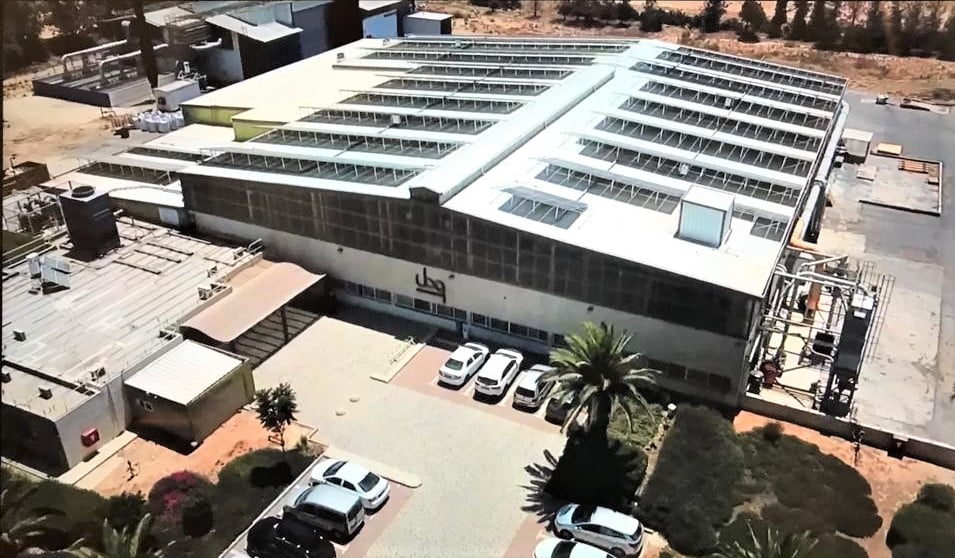
In a September interview with Bigio, the CEO told NoCamels that UBQ Materials was a “plastic replacement company,” but also that the converted waste can be used in the construction industry to make bricks, pavement, buildings and more.
SEE ALSO: Israel’s UBQ, Largest McDonald’s Franchise Team Up For Eco-Friendly Restaurant Materials
Bigio also called UBQ Materials a climate positive solution, which he said included an energy-efficient and environmentally sound process where no emissions are produced, no water utilized, and no waste left behind. It saves 11.7 kg of carbon dioxide equivalent emissions per kg. of UBQ produced, he explained at the time.
UBQ, derived from the word “ubiquitous,” has been “transforming waste into a new natural resource” in Israel for a number of years, Bigio told NoCamels. “We’re taking the waste before it goes to the landfill,” he explained. “There’s no technology today that does that.”
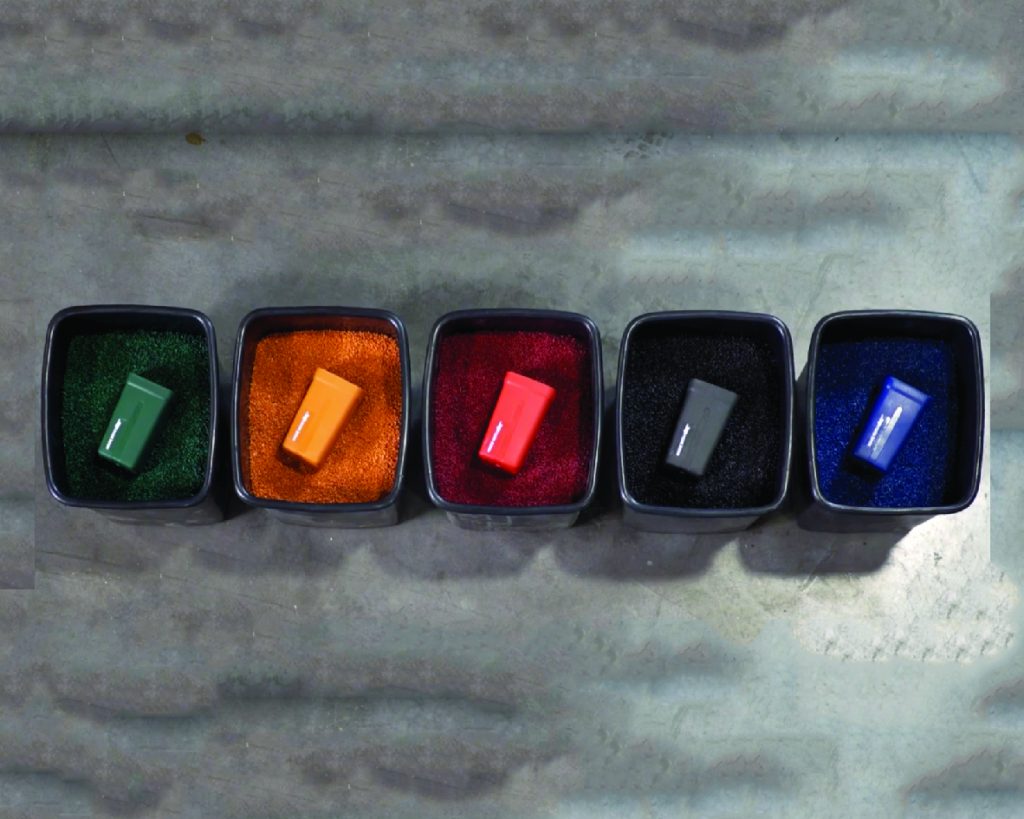
“We don’t need to separate anything,” he said, “We just take the plastics together with the food waste, the cardboard, and paper and convert it into a new climate positive material. This new material can be used by the existing manufacturing industry again and again and recycled many times. It’s an easy way to dispose of the plastic and ease the process through a commercially viable solution.”
Bigio indicated then that manufacturers, retailers, brands, and international conglomerates have been approaching the company as they search for ways to reduce their own company’s carbon footprint.
Related posts
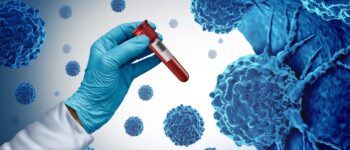
Editors’ & Readers’ Choice: 10 Favorite NoCamels Articles
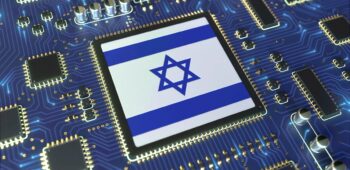
Forward Facing: What Does The Future Hold For Israeli High-Tech?
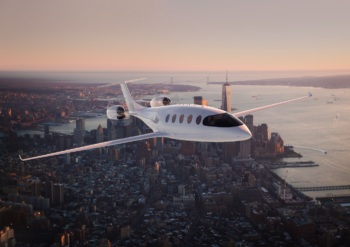
Impact Innovation: Israeli Startups That Could Shape Our Future
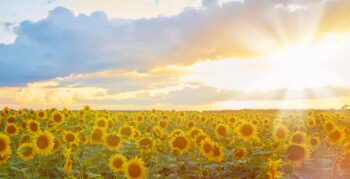
Facebook comments