An Israeli company has developed a nanomaterial-based industrial additives that allow for achieving lightweight and sustainable materials — making it an ideal component for enhancing the properties of plastics used in planes, trains, and yes even automobiles.
The proprietary additives developed by Petah Tikva-based Nemo Nanomaterials can be mass produced in order to supplement a large range of parts. The additives are based on single-walled carbon nanotubes (SWCNT).
The name of the company stems from the concept of Nano Enhanced Material Of the future, which the founders abbreviated to Nemo, while also thinking about Captain Nemo and his journeys where fantastic ideas became a reality.
VP Business Development Jonathan Antebi says he and co-founder and CEO Alexander Zinigrad began to develop the CNTs-based additives after realizing the potential of existing nanomaterial to enhance various kinds of plastics and other industrial material.
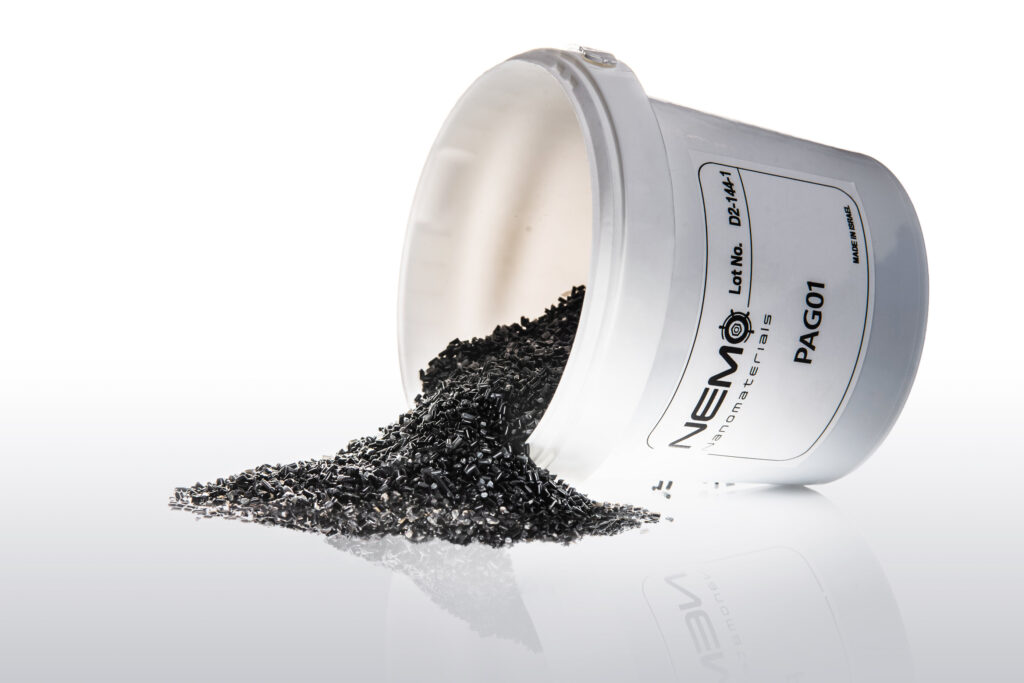
And so in 2018, Antebi, a veteran of the plastic industry, and Zinigrad, an expert in technology transfer and commercialization, began working on developing a scalable technology for manufacturing CNT-based additives. The company R&D is lead by Dr. Ilana Haymov, an experienced researcher in the field of nanomaterials, who joined the company at day one.
“We established Nemo to take the promise of nanocarbons and bring it into industrial reality,” Antebi tells NoCamels.
What they came up with was a product called NemoBLEND – masterbatches (concentrated mixtures) for the plastics industry.
This NemoBLEND can be used in two different types of industrial solutions, Antebi says.
The first is electrical conductivity, for despite not mustering the strength of metal as conductors, the additive are still powerful. They can be used with low levels of electricity, primarily to eliminate the need for a metal layer used as a conductor in many products.
The second is electromagnetic interference. The additives are embedded into different types of plastics to prevent a disruption in the normal operation of electronic devices, something usually caused by electromagnetic signals.
These devices include sensitive products such as radar systems or electronic sensors, which are particularly vulnerable to these signals.
Sign up for our free weekly newsletter
Subscribe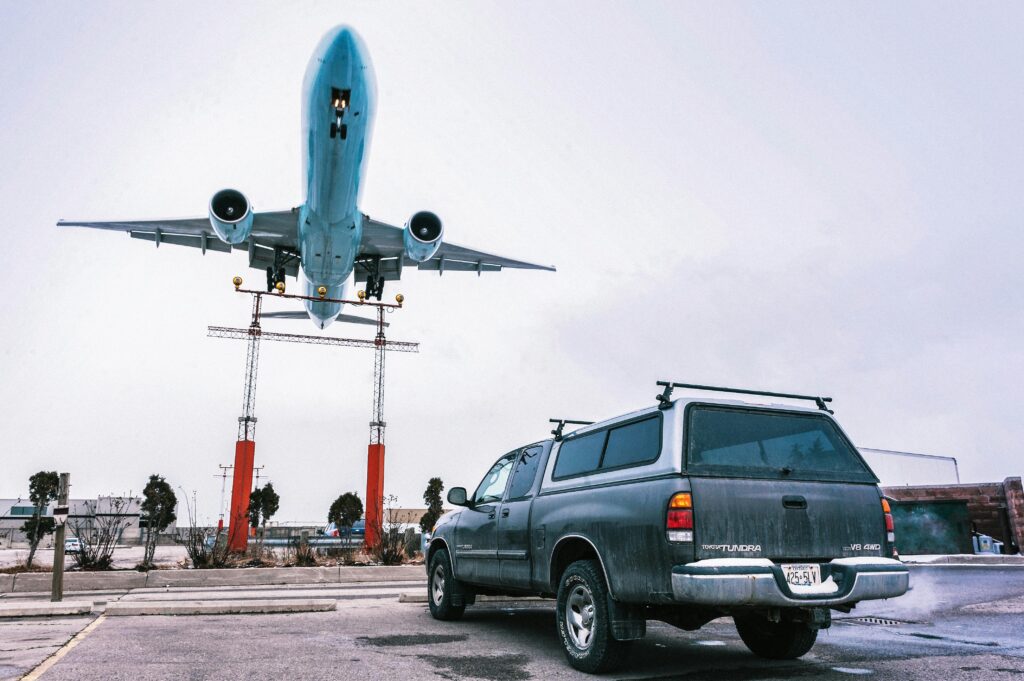
“We enable EMI shielding [preventing electromagnetic disruption] to be embedded in the plastic, plus electrical conductivity, plus the ability to have additional properties like flame retardant and still maintain mechanical properties,” Antebi says.
And while most of electrically conductive products made of plastic are available only in black, NanoBLEND allow Nemo’s customers to produce conductive colored goods.
Nemo jointly won the startup category of the recent Climate Solution Prize, sharing a $1.3 million award with six other nascent Israeli companies as part of an initiative to encourage innovation in this field.
The competition called Nemo a “game changer” in the environmental impact of manufacturing, in particular with regards to metalwork.
NemoBLEND are extremely versatile and can be used in the production of almost any item that includes plastic, explains Antebi. He says Nemo additives can used by the manufacturers of both electric and fuel cars, electronic goods, medical devices, airplanes and locomotives.

Furthermore, he says, Nemo addtives are cost effective for manufacturers as they reduce the amounts of plastic required and bring down production prices. They are also easy to store and maintain their integrity until they are needed.
The startup has received funding from the Israel Innovation Authority (the government branch dedicated to promoting the country’s high-tech sector), as well as private investors. It has also started to market the additives in the United States and in Europe.
Antebi envisions a future for the company in which NemoBLEND is used in every industry, becoming a regular component for multiple manufacturers and credits his colleagues for making a dream into a sustainable reality.
“A team of experts – of engineering, mechanical plastics, chemistry – enabled us to take an idea and convert it into actual up-and-running technology,” he says.
“It enabled us to make a difference.”
Related posts
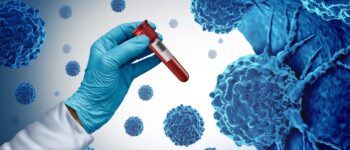
Editors’ & Readers’ Choice: 10 Favorite NoCamels Articles
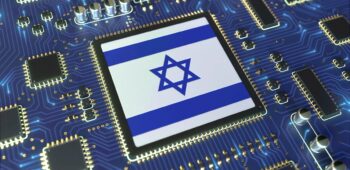
Forward Facing: What Does The Future Hold For Israeli High-Tech?
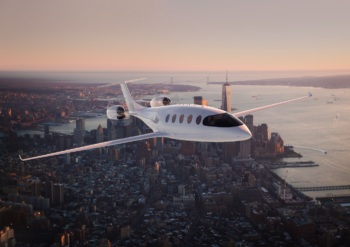
Impact Innovation: Israeli Startups That Could Shape Our Future
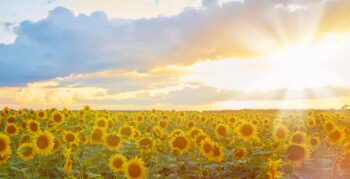
Facebook comments